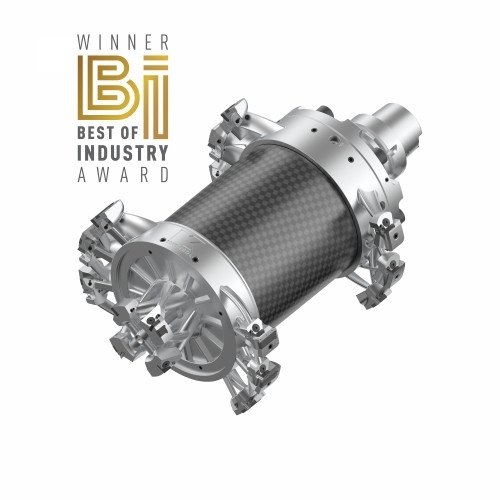
Nagrodzone narzędzie do obróbki otworów stojana, wykonane metodą druku 3D, waży zaledwie 7kg, zapewniając szybką wymianę narzędzi i szybki rozruch centrów obróbczych. To dziś najlżejsze narzędzie do produkcji silników pojazdów elektrycznych.
Kennametal wprowadza nową generację narzędzia, wyprodukowanego metodą druku 3D, przeznaczonego do obróbki otworów w aluminiowych korpusach silników do pojazdów elektrycznych. Charakteryzuje się ono zmodyfikowaną konstrukcją ramion, większą rurą środkową wykonaną z włókna węglowego oraz dalszą redukcją masy o 20 procent w porównaniu z oryginalnym projektem. To złożone narzędzie jest w stanie obrabiać trzy duże średnice w jednym cyklu, skracając czas konfiguracji i obróbki przy produkcji komponentów samochodowych oraz zapewniając największą dokładność i najlepszą jakość powierzchni.
Przeprojektowane narzędzie zdobyło nagrodę Best of Industry MM MaschinenMarkt w kategorii Production and Manufacturing na podstawie głosów czytelników i ekspertów branżowych.
- Ponieważ nasi klienci z branży motoryzacyjnej poszerzają ofertę pojazdów hybrydowych i elektrycznych, nadal odpowiadamy na ich zapotrzebowanie na lżejsze systemy narzędziowe. Wykorzystując zaawansowane techniki produkcyjne, takie jak druk 3D, zmniejszyliśmy wagę o kolejne 20 procent w stosunku do narzędzia pierwszej generacji, jednocześnie poprawiając kontrolę spływu wióra i zwiększając sztywność narzędzia. Innowacje te pomagają naszym klientom pracować szybciej i wydajniej - powiedział Ingo Grillenberger, menadżer produktu z firmy Kennametal.
Fot. Kennametal Inc.
Komentarze (0)