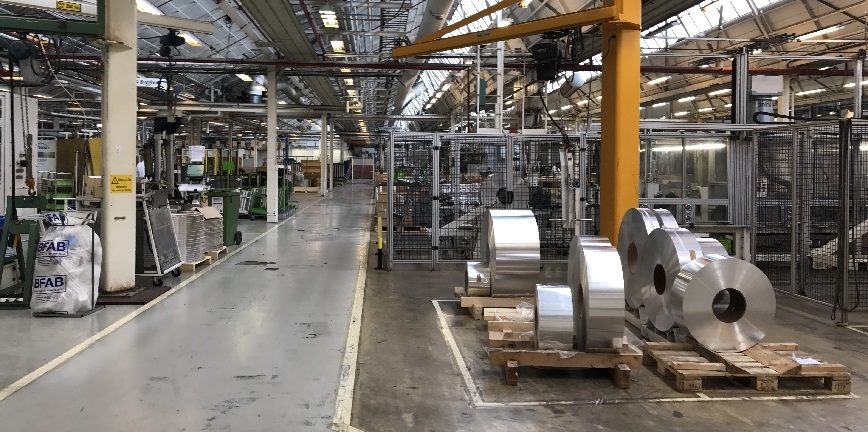
Wyspecjalizowana produkcja od etapu płaskiej taśmy aluminium, z której powstaną rurki, do całego modułu chłodzącego. Kilkusetgodzinne testy przeprowadzone w warunkach ogromnych różnic temperatur, ciśnienia i wilgotności. Tak powstają chłodnice wody, powietrza i oleju TitanX.
Ich odbiorcami są najwięksi producenci samochodów ciężarowych i autobusów, ale są one także dostępne dla każdego, najmniejszego nawet warsztatu. W Polsce i w Europie ich dystrybucją zajmuje się firma Highway International z Krakowa, która zaprosiła nas do odwiedzenia zakładu produkcyjnego TitanX w szwedzkim Mjällby. Proces produkcji i samo centrum testowe robią ogromne wrażenie.
TitanX to bardzo wyspecjalizowany producent. Dostarcza chłodnice (wody, powietrza i oleju) tylko do samochodów ciężarowych i autobusów. – Taka wąska specjalizacja pozwala nam zapewnić wysoką jakość przy stosunkowo niskich kosztach – mówi Jérôme Roldes, dyrektor ds. rozwoju TitanX. – Jesteśmy ekspertami w tej dziedzinie, co pozwala nam dostarczać produkty zaawansowane technologicznie.Najnowszy przykład? We wrześniu wyjdzie nasz produkt dla Scanii, gdzie nowoczesny układ chłodzenia obniża zużycie paliwa o 3% – dodaje. Wysiłki inżynierów TitanX w ostatnich latach skierowane są na coraz większą automatyzację produkcji. – Zapewnia to nam wysoką jakość, bo roboty mylą się rzadziej niż ludzie – mówi Roldes.
TitanX dostarcza produkty w zakresie układów chłodzenia głównie na pierwszy montaż. Do klientów firmy należą najwięksi producenci samochodów ciężarowych i autobusów: Mercedes, Scania, Iveco, Volvo. Do tej grupy dołączyć mają wkrótce MAN i DAF. – Wygląda to tak, że producent podaje nam właściwie dwie informacje – jaki ma być odbiór energii oraz ile jest wolnej przestrzeni na układ chłodzenia. Resztą zajmuje się TitanX. Wyliczymy wszystko pod względem termicznym, wytrzymałościowym – opowiada Roldes. Podkreśla, że automatyzacja procesów przynosi skutki. Liczba produktów odsyłanych w ramach gwarancji spadła praktycznie do zera. W grudniu 2016 roku zakończył się proces sprzedaży TitanX do międzynarodowej grupy TATA. Dziś TitanX ma zakłady w Szwecji (dwa), Stanach Zjednoczonych, Meksyku, Brazylii, Chinach i Polsce. Historia firmy, która powstała na bazie zakładów należących do Valeo, produkujących wcześniej pod marką Blackstone, sięga natomiast 1952 roku.
Budowa chłodnicy krok po kroku
Zwiedzanie zakładu produkcyjnego rozpoczynamy w sercu fabryki. Maszyna wypuszczająca rurki aluminiowe do produkcji chłodnic, którą oglądamy, pracuje 24 godziny na dobę przez 7 dni w tygodniu. Rurki powstają z płaskiej taśmy aluminium.
O procesach produkcyjnych opowiada nam Mikael Vyöni – 38 lat temu szeregowy operator maszyn, dziś odpowiedzialny za jakość produktów w całym zakładzie. – Rurka jest najbardziej czułym, wrażliwym elementem chłodnicy. 95% rurek, których używamy do produkcji naszych chłodnic, jest wytwarzanych na miejscu, zaledwie 5% kupujemy z zewnątrz. Kiedy sami produkujemy rurki, możemy być pewni ich jakości – podkreśla nasz przewodnik. W ciągu sekundy powstają dwie standardowe rurki bądź jedna duża. Umieszczone w nich turbulatory zwiększają wydajność. Kolejny etap produkcji to zgrzewanie elementów. Rdzeń chłodnicy poza rurkami tworzą m.in. boczne listwy. Chłodnica jest transportowana do pieca na specjalnej ramie. Bardzo ważna jest precyzja – miejsce uchwytu jest dokładnie wskazane – do 0,1 mm. Chłodnica trafia do pieca, gdzie jest zgrzewana w temperaturze sięgającej 600 stopni Celsjusza.
– Proces zgrzania jest tu kluczowy. Odpowiednia temperatura i odpowiedni czas w stosunku do odpowiedniej wagi gwarantują sukces. Każde niezgrzanie elementów skutkuje poważnym problemem jakościowym – mówi Mikael Vyöni.
Do chłodnicy dołączają kolejne podzespoły. Założenie zbiorników górnego i dolnego to również bardzo ważny etap, na którym elementy te są jeszcze bardzo podatne na uszkodzenia. Teraz chłodnica trafia na pierwsze testy szczelności – czy próżnia w określonym czasie utrzyma się wewnątrz? Tak jest w 99,8% testowanych chłodnic. Temu testowi poddawane są wszystkie chłodnice w zakładzie. To już ostatnie kroki przed stworzeniem pełnego modułu chłodzącego. Takich linii produkcyjnych w Mjällby jest dziewięć.
Wieloetapowe badania w centrum testowym
W centrum testowym zakładu w Mjällby przeprowadzane są badania wytrzymałościowe chłodnic na drgania, korozję i ciśnienie, są badania termiczne, do dyspozycji pracowników jest tunel aerodynamiczny. Wizytę tutaj zaczynamy od testów wibracyjnych.
- Teraz badamy odporność na wibracje. Mamy dwa urządzenia, które symulują wibracje samochodu w trasie. Ich częstotliwość można ustalić na poziomie nawet 250 Hz, a co ciekawe, taki test wibracyjny trwa nawet 250 godzin – opowiada Magnus Nillson, ekspert firmy ds. testów produktów.
Kolejne miejsce to testy ciśnieniowe. Do tych badań chłodnice wypełnione są glikolem. Ciśnienie podczas testu to przedział od 0 do 400 kPa. Płyn podany do chłodnic ma temperaturę w zakresie od -12 do +100 stopni Celsjusza. W ich trakcie następuje od 2 do 3 tysięcy cykli zmian tej temperatury. Oczywiście nie ma potrzeby, by tak szczegółowym testom poddawać wszystkie chłodnice. Tutaj badane są prototypy, a także pierwsze produkty już zatwierdzone dla klientów. Trafiają tu też losowo wybrane chłodnice z masowej produkcji. Chyba najbardziej widowiskowym elementem wyposażenia centrum testowego są tunele aerodynamiczne, dla większych chłodnic poziome, dla mniejszych pionowe. Tu można regulować temperaturę, ale też stopień wilgotności, prędkość podawanego powietrza. Finalnie stworzone warunki są bardzo zbliżone do drogowych. I mogą być, dokładnie jak te drogowe, bardzo zmienne. Jak poradzi sobie moduł chłodniczy, który jest tu zamontowany już jak w samochodzie ciężarowym? Maksymalna temperatura, którą można tu osiągnąć, to 280 stopni Celsjusza. W Mjällby jest też stanowisko do badań odporności na korozję.
– Producenci samochodów, dla których produkujemy chłodnice, określają, w jakich parametrach chcą przetestować swój produkt. Podają ciśnienie, wilgotność, zakres temperatur, a nawet szybkość wiatru i przemieszczającego się samochodu. Wszystko jesteśmy w stanie zasymulować i wydać dane w rzeczywistych warunkach użytkowania samochodu – dodaje Magnus Nillson.
Komentarze (2)