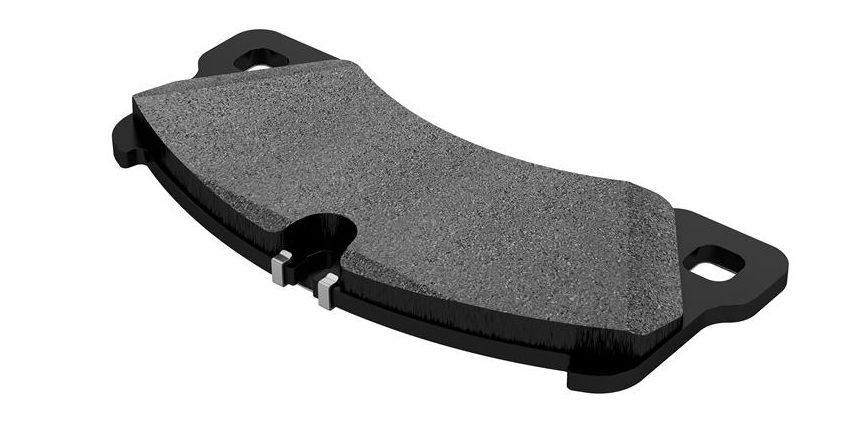
Silnik, kierownica, ogumienie i klocki hamulcowe to jedne z części, które od samego początku towarzyszą historii motoryzacji. Mimo upływu lat ich podstawowe funkcje pozostały niezmienne, jednak rozwój technologiczny sprawił, że niemal każdy element pojazdu przeszedł prawdziwą rewolucję dostosowując się do wymagań stawianych przez rynek. Doskonałym przykładem są klocki hamulcowe, które na przestrzeni ponad 100 lat ewoluowały z drewnianych bloczków obitych skórą do testowanych w warunkach laboratoryjnych mieszanek ciernych.
Historia klocków hamulcowych sięga czasów, gdy podstawowym środkiem lokomocji były pojazdy konne. Proces hamowania odbywał się poprzez dociskanie drewnianego klocka do koła za pomocą specjalnej dźwigni. Co ciekawe, ta technologia była również wykorzystywana w początkowej fazie rozwoju motoryzacji. Karl Benz w swoich pierwszych konstrukcjach pojazdów mechanicznych stosował m.in. drewniane klocki obite skórą.
Kolejnym etapem był rozwój materiałów ciernych, czyli mieszanki będącej bazą współczesnych klocków hamulcowych. Pierwsze z nich powstały pod koniec XIX wieku i składały się z bawełny nasycanej lepkimi substancjami tzw. bitumami. Niestety w stosunkowo niskiej temperaturze 150 °C ulegały rozkładowi, przez co traciły swoje właściwości cierne i wytrzymałościowe. W rezultacie po pewnym czasie bawełna została zastąpiona przez tkaninę azbestową zbrojoną drutem mosiężnym. Odporność termiczna, elastyczność, właściwości cierne oraz kompatybilność ze środkami wiążącymi sprawiły, że azbest stał się głównym składnikiem materiałów ciernych na kolejnych kilka dziesięcioleci. Dopiero w związku z jego rakotwórczymi właściwościami, w latach 70 zaczęto zastępować ten składnik mieszaniną różnych włókien m.in.: włókna szklanego, wełny mineralnej, włókien syntetycznych, wełny stalowej, włókna stalowego oraz włókien naturalnych.
Na drodze ku współczesności
Dynamiczny rozwój motoryzacji na przestrzeni ostatnich czterech dekad wymusił na producentach części motoryzacyjnych liczne modyfikacje, związane ze zwiększeniem rozmiaru i osiągów pojazdów. Przykładowo masa samochodu kompaktowego wzrosła w tym czasie o około 40 - 50 %. Zwiększyły się też prędkości maksymalne oraz przyczepność opon pozwalająca na większe opóźnienia hamowania.
- Klocki hamulcowe przez ostatnie kilkadziesiąt lat na pozór niewiele się zmieniły. Wizualnie wyglądają podobnie. Są złożone z metalowej blaszki nośnej i materiału ciernego. Dzisiaj częściej niż kiedyś są wyposażone w nakładki antypiskowe tzw. shimy i czujniki zużycia - elektryczne lub akustyczne. Najłatwiej spostrzec różnicę w ich rozmiarach. Na przykład przedni klocek VW Golfa I miał powierzchnię około 30 cm2, a objętość materiału ciernego wynosiła około 21 cm3. Ostatni model Golfa VII posiada hamulce przednie wyposażone w klocki o powierzchni około 62 cm2 i objętości materiału około 74 cm3 - tłumaczy Tomasz Orłowski, kierownik w Dziale Badań i Rozwoju Lumag, odpowiedzialny za rozwój klocków hamulcowych Breck.
Coraz więcej, coraz szybciej, coraz bezpieczniej
Wprowadzanie na rynek przez producentów samochodów coraz większej liczby modeli, w coraz krótszym czasie, wymusza na producentach układów hamulcowych skrócenie także czasu potrzebnego na opracowanie nowych produktów. Nie byłoby to możliwe bez nowoczesnych metod badawczo-rozwojowych i obliczeniowych umożliwiających realizację zaawansowanych testów laboratoryjnych, które w dużym stopniu zastępują prób jezdnych. Testy na drogach publicznych, torach wyścigowych lub w ekstremalnych warunkach górskich są dopiero ostatnim etapem poprzedzającym wprowadzenie produktów na rynek.
Zwiększanie oczekiwań i wymogów dotyczących układów hamulcowych sprawia, że materiały cierne konstruuje się i bada w oparciu o szereg zmiennych. Wśród najważniejszych należy wymienić odpowiednio wysoki i stabilny współczynnik tarcia, niskie zużycie tarczy i materiału ciernego, brak wibracji, pisków i różnych innych hałasów pochodzących od hamulców. Oddzielną kwestią są wysokie wymagania w zakresie ekologiczności produktów, a więc brak w składzie mieszanki ciernej metali ciężkich, antymonu, a w niedalekiej przyszłości również miedzi.
- Zmiany dokonywane w ostatnich latach w procesie tworzenia i produkcji klocków hamulcowych, do momentu rozpoczęcia ich użytkowania, dla wielu osób pozostają na pierwszy rzut oka niezauważalne, gdyż ograniczają się do składu mieszanki ciernej. Jednak pewne aspekty można dostrzec dość szybko. Ciekawym przykładem są montowane w pojazdach z segmentu premium oraz SUV-ach klocki hamulcowe z przymocowanymi do blaszki nośnej specjalnymi ciężarkami, których jedyną funkcją jest zmiana częstotliwości drgań własnych klocka powodująca eliminacje lub znaczną redukcje pisków hamulca – dodaje Tomasz Orłowski.
Przez lata zmianie uległ nie tylko wygląd i skład materiałów ciernych, ale również sam proces produkcyjny. Obecnie często stosuje się nowe technologie dotyczące obróbki cieplnej, na przykład tzw. schorching (krótkie i powierzchniowe nagrzewanie powierzchni materiału ciernego do temperatur rzędu 600 - 800 °C), który zwiększa odporność na zjawisko „fadingu”, czyli gwałtownego zmniejszenia się skuteczności hamownia przy szybko rosnącej temperaturze hamulców. Dodatkowo nowe generacje produktów wymagają odpowiedniego materiału łączącego blachę nośną z materiałem ciernym (tzw. międzywarstwę), która musi mieć odpowiednią wytrzymałość mechaniczną, ale również dobre właściwości elastyczne (tłumienie pisków) i termiczne (bariera cieplna).
Pomimo tych wszystkich zmiennych oraz znacznie krótszego czasu potrzebnego na opracowanie nowych mieszanek ciernych do coraz liczniejszych i nowocześniejszych modeli samochodów - doświadczenie, zdobywana przez lata wiedza oraz nowe metody i urządzenia badawcze renomowanych producentów klocków hamulcowych sprawiają, że współczesne klocki hamulcowe są bardzo nowoczesne i ekologiczne.
Komentarze (0)