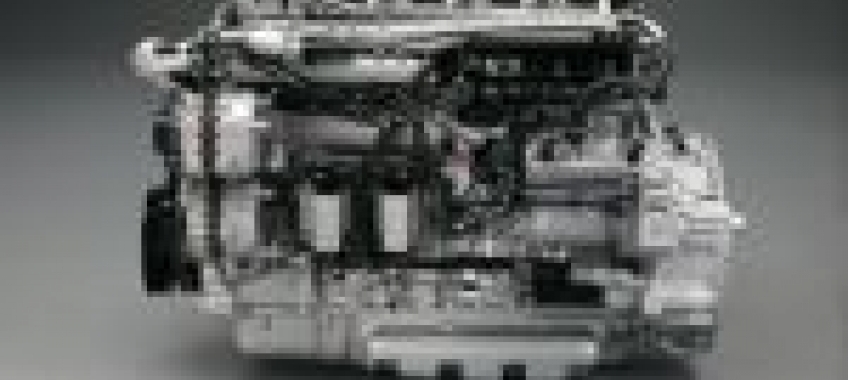
w układzie Common Rail
Samochody z układem Common Rail krążą po naszych drogach już ponad 8 lat. Ich liczba niezmiennie się zwiększa. Zwiększa się również i liczba usterek w tych pojazdach. Jeszcze do niedawna naprawa samochodu z układem Common Rail kojarzyła się przeważnie z naprawą pompy wysokiego ciśnienia lub wtryskiwaczy. Z biegiem czasu do tych usterek dołączają uszkodzenia innych elementów silnika związanych ze sterowaniem jego pracy. Dotyczy to przede wszystkim czujników silnika.
Czujniki - “oczy” i “uszy” nowoczesnego silnika” (zdjęcie z publikacji SCANIA).
W zależności od marki i rodzaju pojazdu może posiadać on różną liczbą czujników, niemniej silniki z układem Common Rail zawsze posiadają pewną grupę czujników, bez których wysterowania ich pracą byłoby niemożliwa. Do tej grupy zaliczane są czujniki:
- położenia wałka rozrządu;
- położenia wału korbowego;
- prędkości jazdy;
- spalania stukowego
- położenia pedału gazu;
- położenia zaworu recyrkulacji spalin.
- temperatury silnika;
- temperatury cieczy chłodzącej;
- temperatury paliwa;
- temperatury powietrza;
- przepływomierz;
- ciśnienia w kolektorze dolotowym.
Naprawa układów Common Rail bez znajomości zasad działania tych poszczególnych czujników może być bardzo uciążliwa, czasami wręcz niemożliwa. Warto więc przypomnieć te podstawowe informacje.
Czujniki położenia wałka rozrządu i wału korbowego są najważniejszymi czujnikami w silniku. Mogą one przekazywać do komputera pokładowego informacje związane nie tylko z położeniem wałków, ale również i inne związane z określeniem górnego martwego punktu (GMP), pracy określonego cylindra lub prędkości obrotowej silnika. Występują dwa rodzaje tych czujników, czujniki indukcyjne i hallotronowe (zwane czujnikami Halla). Obydwa rodzaje czujników współpracują z odpowiednim kołem zębatym. Czujniki indukcyjne nie są zasilane. W wyniku zmiany szerokości szczeliny powietrznej pomiędzy pracującymi elementami w czujniku indukcyjnym odbywa się wyindukowanie napięcia w cewce czujnika. Czujnik Halla z kolei w trakcie pracy przy zmianie szerokości szczeliny zeruje sygnał pomiarowy. Dlatego musi być zasilany. Wizualnie czujniki indukcyjne można odróżnić od czujników Halla przez liczbę styków na wtyczce. Jak wynika z ich zasad działania, czujnik indukcyjny ma dwie wtyczki, Halla – trzy. Do określenia zadanego położenia wałka wykorzystywane są zmiany regularności poszczególnych wypustów na kołach zębatych. Zaburzenie regularności sygnału pomiarowego przekazywanego z czujników położenia do komputera pokładowego rozpoznawane jest jako impuls sterujący.
Poprawna praca układu dolotowego i wylotowego jest niemożliwa bez właściwej kontroli (obrazek z publikacji SCANIA).
Zwiększenie wymagań producentów pojazdów do jakości i funkcjonalności czujników silnikowych doprowadziło do powstania nowej generacji czujników Halla. Czujniki te wyposażone są w mikrokontroler i interfejs cyfrowy. Mogą być one dodatkowo wyposażone w czujnik temperatury, zespół obwodów kompensacyjnych oraz pamięć wewnętrzną EEPROM. Precyzja, elastyczność konfiguracji i pracy tych czujników już wkrótce zostaną w pełni wykorzystane w nowych opracowaniach konstruktorskich. Niewłaściwa praca czujników położenia może mieć wpływ na brak możliwości uruchomienia silnika, utrudniony rozruch na zimnym i ciepłym silniku, przerywaną lub “stukową” pracę silnika. Czujnik prędkości jazdy (prędkości liniowej samochodu) montowany jest zazwyczaj w skrzyni biegów. Czujnik ten składa się z rotora z zamocowanymi na nim magnesami, czujnika Halla i układu elektronicznego. Ocena sygnału wyjściowego czujnika prędkości jazdy odbywa się poprzez ocenę jego częstotliwości, ponieważ na jeden obrót rotora zawsze przypada stała ilość impulsów wyjściowych. Usterka czujnika prędkości jazdy nie wymaga diagnostyki serwisowej, ponieważ jest w większości przypadków widoczna dla użytkownika pojazdu z odczytów prędkościomierza. W charakterze czujników spalania stukowego najczęściej wykorzystywane są akcelerometry. Łączone są z odpowiednimi detektorami dokonującymi analizy widmowej lub czasowej sygnału pochodzącego z czujnika. Analiza widmowa polega na ustaleniu właściwości sygnału w oparciu o charakter jego widma. Jest to analiza instrumentalna posiadająca bardzo wysoki stopień dokładności i wiarygodności. Analiza czasowa odbywa się poprzez obliczanie odpowiedzi czasowej układu w określonym przez sterownik czasie. Analiza sygnału jest niezbędna, ponieważ pasma detekcji spalania stukowego znajdują się w obszarze występowania różnorodnych sygnałów akustycznych: eksplozji mieszanki w cylindrze, drgań karoserii, naprężeń głowicy i śrub mocujących itp. W trakcie pracy wewnątrz czujnika powstają drgania przekazywane na ruchomy pierścień. Pierścień pod ich wpływem naciska na element piezokwarcowy, który generuje sygnał pomiarowy. Częstotliwość pracy czujnika mieści się pomiędzy 1 a 20kHz. Niewłaściwa praca czujnika stukowego może mieć wpływ na nierówną, głośną lub “twardą” pracę silnika. Czujnik położenia pedału gazu w dowolnym wykonaniu konstrukcyjnym jest to zespół składający się z dwóch potencjometrów połączonych ze sobą. Ważne jest to, że potencjometry te mają nieco różne charakterystyki pozwalające komputerowi pokładowemu na wprowadzenie odpowiednich korekt pracy silnika przy uszkodzeniu jednego z nich. Potencjometry obrotowe wykorzystywane są również i jako czujniki położenia zaworu recyrkulacji spalin (EGR). Połączone są z ośką klapy zaworu. W ten sposób dowolna zmiana położenia klapy jest bezbłędnie odczytywana przez komputer pokładowy.
Nowoczesne czujniki położenia pedału gazu są zespolone z samym pedałem oraz tworzą niezawodne i precyzyjne narzędzie do sterowania silnikiem.
Temperatura w silniku mierzona jest czujnikami temperatury działającymi na zasadzie rezystora cieplnego (termistora). Praca czujnika temperatury polega na zmianie rezystancji czujnika przy wzroście jego temperatury. Zmiana rezystancji termistora może mieć dodatni współczynnik temperaturowy (PTC), przy którym wzrost temperatury czujnika powoduje wzrost jego rezystancji lub ujemny (NTC), przy którym wzrost temperatury powoduje jej zmniejszenie. Czujniki temperatury zasilane są z jednostki sterującej napięciem 5 V. Uszkodzenia czujników temperatury w różnych układach silnika mogą powodować: utrudniony rozruch, zwiększone zużycie paliwa, nierówną lub niestabilną pracę silnika. Jeżeli komputer pokładowy można nazwać “mózgiem samochodu”, a układ paliwowy ”sercem”, to przepływomierz powierza bez wątpienia można nazwać jego “płucami”. Bez poprawnej pracy przepływomierza niemożliwe jest uzyskanie przez samochód nominalnej mocy, przyśpieszenia, właściwego spalania oleju napędowego itp. Często występujące objawy złej pracy przepływomierza to: dymienie ma czarno, biało lub niebiesko; wibracja pracy silnika, przerywana praca silnika. Przepływomierz jest urządzeniem pomiarowym, służącym do pomiaru objętości lub przepływającego powietrza w układzie dolotowym. Przepływomierze umownie można podzielić na dwie grupy: klapowe i termoanemometry. Przepływomierze klapowe dokonują bezpośredniego pomiaru objętości przepływającego przez ich przestrzeń powietrza poprzez wychylenie ruchomej klapy połączonej z potencjometrem. Zmiana rezystancji potencjometru jest proporcjonalna do wychylenia klapy, czyli do ilości mierzonego powietrza. W celu wprowadzenia korekty temperaturowej w przepływomierzach klapowych dodatkowo montowane są czujniki temperatury. Do podłączenia służą pięciopinowe złącza. Trzy piny odpowiadają za połączenie z potencjometrem, zaś dwa pozostałe z czujnikiem temperatury. Konstrukcja termoanemometrów zawiera tak zwany “gorący element” chłodzony przepływającym przez przestrzeń przepływomierza powietrze. Nagrzewanie “gorącego elementu” odbywa się poprzez przepuszczenie przez niego prądu elektrycznego. Ilość przepływającego powietrza jest związana z szybkością chłodzenia, w związku z czym można ją określić przez natężenie prądu niezbędne do utrzymania stałej temperatury “gorącego elementu”. W celu zapewnienia wysokiej dokładności pomiaru temperatura “gorącego elementu” ustawiana jest na 130C powyżej temperatury otoczenia. W charakterze “gorącego elementu” w termoanemometrach wykorzystywane są druty lub płytki. Napięcie zasilania tych przepływomierzy wynosi od 9 do 16 V, napięcie sygnału wyjściowego znajduje się pomiędzy 0,5 a 4,6 V. Zastępczym rozwiązaniem do pomiaru powietrza w układzie dolotowym samochodu jest zastosowanie w nim czujnika ciśnienia. Mierzy on w trybie ciągłym ciśnienie zasysanego przez silnik powietrza oraz ciśnienia atmosferycznego. Pomiar ilości zasysanego powietrza odbywa się na zasadzie powiązania tabelarycznego bieżącej wielkości ciśnienia w układzie dolotowym z jego temperaturą i prędkością obrotową wału korbowego. Wbrew pozorom konstrukcja czujnika nie jest zbyt prosta. Ciśnienie dostarczane do czujnika przetwarzane jest na sygnał elektryczny przez silikonowy miniukład. W miniukład wtopiono piezorezystory, czułe na działanie ciśnienia. Znajduje się w nim również komora próżniowa pełniąca rolę membrany. Odkształcenie piezorezystorów pod działaniem ciśnienia powoduje zmiany ich oporności. Powoduje to z kolei zmianę napięcia zasilania. Proporcjonalna zależność pomiędzy przyrostem ciśnienia a przyrostem napięcia sygnału pomiarowego pozwala na dokładne określenie wielkości ciśnienia dostarczanego do czujnika.
Siergiej Jaroszenko
Komentarze (0)