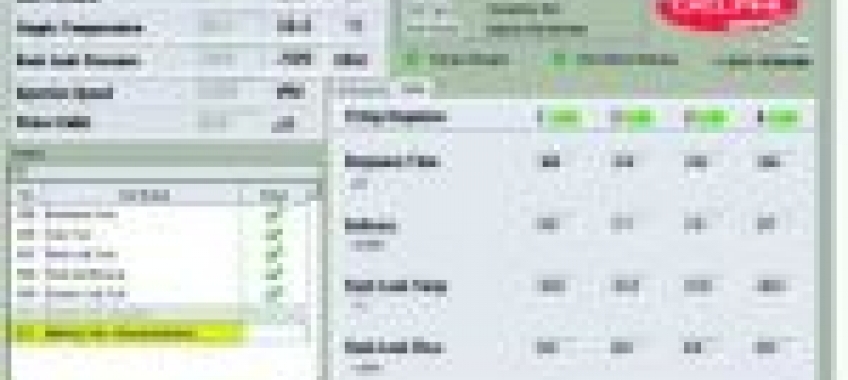
podzespołów układów CR
Różnica w definicjach diagnostyki i testowania podzespołów układów zasilania silników wysokoprężnych jest oczywista, niemniej w praktyce te dwa pojęcia często się przeplatają i granica pomiędzy nimi się zaciera. Dzieje się tak nie na skutek wadliwych określeń, lecz sposobu ich zastosowania. Zastosowanie tych pojęć często jest podciągane do posiadanego przez serwisy samochodowe wyposażenia, zamiast właściwych procedur. Warto przypomnieć, iż termin diagnostyka pochodzący z języka greckiego, gdzie diagnosis oznacza rozpoznanie, rozróżnianie, osądzanie, a diagnostike techne – sztukę stawiania diagnozy. Można więc zdefiniować diagnostykę techniczną jako ocenę stanu technicznego badanego urządzenia technicznego poprzez badania własności procesów roboczych i towarzyszących ich pracy. W odniesieniu do motoryzacji diagnoza zazwyczaj dotyczy zarówno oceny stanu technicznego samochodu, jak i jego podzespołów (układów). Obejmuje ona również prognozę zmian stanu, jak i określenie przyczyn zmian. Nie dotyczy natomiast oceny przyczyn powstania tych zmian. Innymi słowami mówiąc, podczas diagnozowania samochodu z układem Common Rail, stosując właściwe procedury i urządzenia, serwis samochodowy powinien odpowiedzieć na pytania:
- czy samochód klienta może być dalej eksploatowany w obecnym stanie i jeżeli tak, to jak długo;
- który podzespół samochodu uniemożliwia jego dalszą eksploatację i dlaczego właśnie ten, a nie inny.
Stosowane procedury zazwyczaj powinny być oparte na zgromadzoną wiedzę teoretyczną, doświadczenie i posiadane wyposażenie, niemniej ramowy schemat wygląda następująco:
- przygotowanie samochodu do wykonania czynności diagnostycznych;
- sprawdzenie kodów błędów w komputerze pokładowym;
- sprawdzenie szczelności dynamicznej i statycznej wtryskiwaczy;
- w razie konieczności diagnostyka wtryskiwaczy poza silnikiem samochodu;
- sprawdzenie szczelności zasobników CR (w przypadku zasobników zaworowych);
- sprawdzenie wydajności i szczelności pompy wysokiego ciśnienia;
- sprawdzenie zawartości filtra paliwa i zbiornika;
- sprawdzenie pracy pozostałych podzespołów samochodu, praca których jest pośrednio lub bezpośrednio związana z układem Common Rail;
- sprawdzenie poprawności pracy komputera pokładowego.
Ramowy schemat diagnostyki i naprawy samochodu z układem Common Rail.
Podany schemat pozwala na określenie właściwych dla danego serwisu procedur oraz ich elastyczne wdrożenie w działalność każdego serwisu samochodowego.
Wyposażenie niezbędne do zastosowania tego schematu to:
- elektroniczne urządzenie diagnostyczne;
- zestaw do bezpośrednich pomiarów szczelności i ciśnienia w układach CR;
- zestaw zaślepek gniazd elektrozaworów;
- zestaw zaślepek króćców wysokiego ciśnienia;
- tester wtryskiwaczy CR;
- multimetr;
- oscyloskop;
- klucze i przyrządy specjalistyczne, właściwe dla danej marki samochodu.
Po określeniu wadliwego podzespołu następuje jego wymiana lub naprawa. Wymiana podzespołów na nowe jest kwestią odpowiedniego zaopatrzenia, naprawa zaś opiera się o współpracę z serwisem specjalistycznym. Montaż nowych lub naprawionych podzespołów Common Rail wiąże się przeważnie z kilkoma głównymi zasadami:
- zachowaniem czystości;
- odpowiednią kolejnością montażu podzespołów;
- właściwym przygotowaniem miejsc montażowych;
- zastosowaniem wymaganych momentów sił;
- stosowaniem wyłącznie oryginalnych filtrów paliwa. Pod pojęciem oryginalny należy rozumieć filtr z oznaczeniem producenta pojazdu lub układu zasilania;
- odpowietrzeniem układu;
- kontrolę końcową.
Ostatnia zasada jest o tyle ważna, że po pierwsze jest zapełnieniem jakości wykonanej pracy, a po drugie wiąże się z koniecznością wykonania testu drogowego lub jazdy próbnej. W trakcie tej jazdy komputer pokładowy dostosowuje sterowanie podzespołami do parametrów silnika, wyrównując jego pracę i zapełniając odpowiednie osiągi.
W odróżnieniu od diagnostyki, testowanie podzespołów jest określonym działaniem przeprowadzanym w kontrolowany sposób w celu sprawdzenia zgodności parametrów technicznych podzespołów z wymaganiami producenta. Testowanie umownie można podzielić na weryfikację stanu podzespołów oraz ich walidację. Weryfikacja stanu podzespołów pozwala określić nie tylko możliwość dalszej eksploatacji części zamiennych przedmiotowych podzespołów, ale również i przyczyny powstania ich usterek. Walidacja z kolei jest procesem związanym z bezpośrednim porównaniem mierzonych parametrów badanego podzespołu z test-planem producenta.
Testowanie pomp wysokiego ciśnienia Siemens Common Rail odbywa się w trybie półautomatycznym.
Dlaczego, wbrew krążącym na rynku opiniom, należy zlecać naprawy podzespołów układów Common Rail serwisom specjalistycznym posiadającym autoryzację ich producenta? Przede wszystkim dlatego, że tylko te serwisy mogą wykonać technologiczne testowanie podzespołów po ich naprawie i co za tym - idzie zabezpieczyć właściwe wsparcie posprzedażne oraz ustawowe terminy gwarancyjne. Wiąże się to z trzema czynnikami: wyposażeniem, przeszkoleniem personelu oraz posiadaniem wymagań producenta do parametrów naprawionych podzespołów.
Odczyty parametrów testowania pomp Delphi Common Rail ze stołu probierczego Hartridge AVM2-PC.
W ostatnim czasie na rynku pojawiło się sporo urządzeń oferowanych do naprawy podzespołów Common Rail, czyli w założeniu urządzeń testowych (probierczych). Nawet taki potentat jak firma Bosch uległ pokusie sprzedaży urządzenia diagnostycznego do wtryskiwaczy EPS-200 jako urządzenia do ich naprawy. Główną różnicą urządzeń diagnostycznych i testowych jest możliwość wykonania walidacji przy wykorzystaniu urządzeń testowych i jej brak przy zastosowaniu urządzeń diagnostycznych. W charakterze przykładu można podać proces testowania pomp i wtryskiwaczy firmy Delphi.
Testowanie pomp wysokiego ciśnienia Delpi Common Rail, poza wydatkiem i szczelnością, możliwym do pomierzenia na innych urządzeniach niż wymagane przez Delphi, wymaga również sprawdzenia podciśnienia na zwężce Venturiego, mapy temperaturowej oraz pracy elektrozaworu sterującego i bezpieczeństwa. Lekceważenie sprawdzenia tych elementów bezpośrednio wiąże się z możliwością usterki całego układu w krótkim okresie jego eksploatacji po naprawie. Brak z kolei wygenerowania po naprawie wtryskiwaczy Delphi Common Rail nowego kodu C2I może w praktyce oznaczać kłopoty z właściwą pracą silnika, a nawet doprowadzić do jego uszkodzenia. Podobnie sytuacja wygląda i u innych producentów, takich jak Bosch (kodowane wtryskiwacze), Siemens (powiązania czasowo-wydajnościowe) i Denso (system powiązań obciążeniowych). Wybierając odpowiedniego partnera w postaci serwisu specjalistycznego, warto uzyskać odpowiedzi na kilka prostych pytań:
- czy naprawione podzespoły spełniają wymagania jego producenta;
- na podstawie czego odbywało się testowanie naprawionych podzespołów.
Generowanie kodów C2I do wtryskiwaczy Delphi jest procesem automatycznym, zawierającym ciągłe odczyty wszystkich parametrów pracy badanych wtryskiwaczy.
Pytania te zadane w tej czy innej formie są niezbędne, ponieważ tworzą podstawę do zapewnienia końcowego wyniku naprawy samochodu. Brak pewności partnera w większości przypadków doprowadza do sytuacji spornych, niemożliwych do natychmiastowego rozwiązania. Skutkiem jest przedłużenie czasu napraw, zwiększone koszty oraz utrata reputacji serwisu.
Sprawdzenie dawki przepływu wytwarzanego podciśnienia, ciśnienia przetłaczania i mapy temperatur tworzy podstawę testowania pomp Delphi Common Rail.
W tym artykule zostały zawarte przypomnienia, co należy zrobić w celu wykonania właściwej diagnostyki i naprawy układów Common Rail, natomiast odpowiedź na pytanie jak, możecie Państwo znaleźć na szkoleniach organizowanych przez “Nowoczesny Warsztat”, na które serdecznie zapraszamy.
Siergiej Jaroszenko
Komentarze (0)