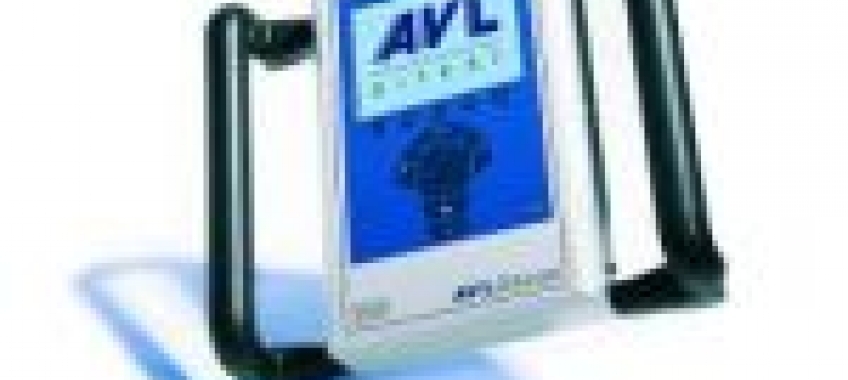
Wprowadzenie standardów diagnostyki pokładowej, poza aspektami ochrony środowiska, usprawniło proces diagnostyki i naprawy elementów oraz podzespołów emisyjnie krytycznych, ujednoliciło i znormalizowało procedury diagnostyczne, a także metody komunikacji z jednostką diagnostyczną w pojeździe.
Diagnostyka drugiej generacji znana jest pod nazwami OBD II (z ang. On Board Diagnostic II – obowiązuje na rynku amerykańskim od 1996 r.) i EOBD (European On Board Diagnostic) w krajach Unii Europejskiej wprowadzona w 2000 r.
W Polsce przepisy związane z diagnostyką pokładową obowiązują dla pojazdów wyprodukowanych po 1 kwietnia 2001 r. Układ diagnostyki pokładowej umożliwia wykrywanie uszkodzeń emisyjnych w ich wczesnej fazie rozwoju, kiedy wywołana nimi emisja nie przekracza dopuszczalnych limitów i powoduje jeszcze niewielkie straty dla środowiska. Ciągłe monitorowanie systemów i procesów w silniku umożliwia szybkie wykrycie uszkodzenia lub nieprawidłowej pracy, powodującej nadmierną emisję składników toksycznych spalin oraz powiadamianie o niej kierowcy. System diagnostyki pokładowej jest oprogramowaniem analizującym parametry pracy silnika, które sprawdza czy:
- nie występują usterki mogące uszkodzić katalizator,
- silnik i jego układy pracują tak, że nie powodują emisji składników toksycznych ponad dopuszczalną normę,
- wszystkie elementy układów sterujących silnika, katalizator i sondy lambda są sprawne.
Komunikacja z jednostką sterującą w pojeździe możliwa jest dzięki urządzeniom diagnostycznym zwanymi skanerami. Podłączane są przez znormalizowane złącze 16-pinowe. Jednym z takich urządzeń jest tester AVL DiScan 8000 (rys. 1).
Podstawowym pojęciem normy OBD jest pojęcie monitora diagnostycznego. Jest to procedura diagnostyczna, której zadaniem jest wykrywanie uszkodzeń elementu lub układu mającego wpływ na emisję z systemu zasilania lub wylotowego.
Nadzór nad przebiegiem procedur monitorujących, realizowanych sprzętowo i programowo sprawuje sterownik silnika ECU, w którym przechowywane są wyniki testów oraz podejmowane są decyzje o zapaleniu się kontrolki MIL (Malfunction Indicator Lamp) na desce rozdzielczej w przypadku wystąpienia uszkodzenia.
Występują dwa rodzaje monitorów:
n bezwarunkowe, tzw. ciągłe, które nadzorują pracę tych elementów i podzespołów, które muszą być testowane na bieżąco - dowolnych warunkach jazdy. Dotyczy to układu wypadania zapłonów, zasilania paliwem, elementów elektrycznych i elektronicznych;
- warunkowe, tzw. nieciągłe, które uaktywniają się w momencie zakończenia z wynikiem pozytywnym działania innych monitorów i nadzorują te elementy oraz podzespoły, w których identyfikacja uszkodzeń wymaga dłuższego czasu obserwacji w warunkach reprezentowanych przez określone cykle jezdne.
Szczegółowe warunki uaktywniania danego monitora są definiowane stanem cieplnym i dynamicznym silnika oraz zmiennością tych parametrów w czasie. Za wybór warunków odpowiednich do pracy monitora odpowiedzialny jest producent pojazdu. Monitory generują kody błędów, jednak ich zarejestrowanie w sterowniku następuje dwuetapowo. Usterka, o której informuje kod błędu może zostać sklasyfikowana jako prawdopodobna lub potwierdzona.
Usterka prawdopodobna powstaje w chwili wykrycia pierwszego symptomu uszkodzenia, jeśli tylko dowolny monitor osiągnie negatywny wynik. Wtedy musi zostać zarejestrowany zbiór parametrów określających stan pracy silnika, tzw. “ramka zamrożona”.
Usterka prawdopodobna może przejść w usterkę potwierdzoną przy spełnieniu określonych warunków, np. w kolejnych cyklach jezdnych, podczas nagrzewania się silnika. Może również dojść do sytuacji, gdzie zarejestrowana usterka zostanie skasowana przez sterownik, jeśli podczas takich samych warunków pracy silnika nie zostaną wykryte identyczne symptomy uszkodzeń, które spowodowały wystąpienie usterki prawdopodobnej.
Funkcje, które muszą posiadać skanery dla samochodów z układami diagnostyki pokładowej standardu EOBD, są podzielone na 9 trybów pracy (rys. 2).
Tryb 1 – odczyt ze sterownika silnika parametrów charakteryzujących jego pracę oraz statusów procedur kontrolnych (monitorów). To najważniejszy tryb, gdyż jego informacje określają poprawność działania systemu (rys. 3).
Tryb 2 – dostęp do danych przechowywanych w pamięci sterownika w postaci tzw. “ramki zamrożonej”, zarejestrowanych podczas eksploatacji samochodu, mających wpływ na emisję składników toksycznych spalin (rys. 4).
Tryb 3 – odczyt zarejestrowanych kodów błędów. Kody błędów mogą rozpoczynać się od P0 lub P1. P0 – znormalizowane kody błędów, których oznaczenia i definicje są identyczne dla wszystkich producentów pojazdów; P1 – oznaczenia kodów błędów są znormalizowane natomiast ich definicje są ustalane przez producentów pojazdów (rys. 5).
Tryb 4 – kasowanie kodów błędów i informacji “zamrożonych” zapamiętanych w sterowniku silnika (rys. 6).
Tryb 5 – określa sprawność katalizatora na podstawie analizy sygnałów z czujników tlenu (rys. 7).
Tryb 6 – testowanie procedur diagnostycznych – monitorów warunkowych, tzn. nie pracujących w sposób ciągły (rys. 8).
Tryb 7 – testowanie procedur diagnostycznych – monitorów bezwarunkowych, tzn. pracujących w sposób ciągły. W tym trybie możliwa jest aktywacja poszczególnych podzespołów, elementów wykonawczych.
Tryb 8 – kontrola stanu wyjściowego – do informowania o statusie testów układów i elementów tych układów (wykonany/niewykonany). W tym trybie można odczytać prawdopodobne kody błędów. Aktualnie ten tryb pracy jest rzadko wykorzystywany przez producentów (rys. 9).
Tryb 9 – zapytanie o numer identyfikacyjny pojazdu VIN oraz aktualne dane wersji oprogramowania (rys. 10).
mgr inż. Michał Janowski
janowski@werther.pl
Komentarze (0)