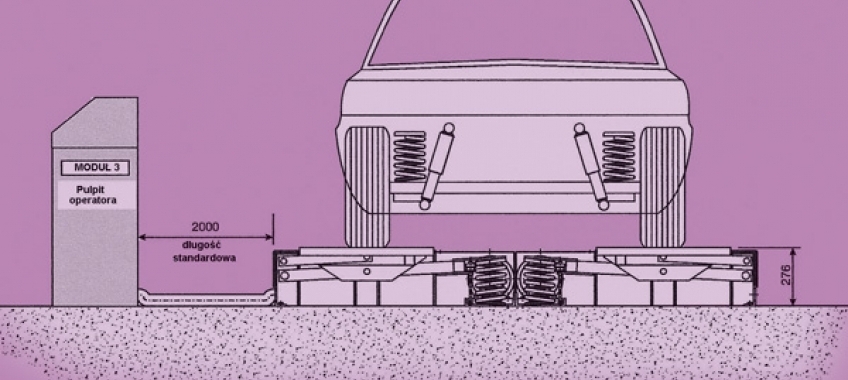
W poprzedniej części artykułu opisano odmiany stacjonarne tych urządzeń. Obecnie zostaną przedstawione mobilne urządzenia do badania zawieszenia metodą drgań wymuszonych oraz przyrządy do badania układów hydraulicznych, wykorzystywane m.in. do kontroli stanu technicznego zawieszenia hydropneumatycznego. Rozwiązanie konstrukcyjne w wersji mobilnej umożliwia usytuowania urządzeń na posadzce stanowiska bez konieczności wykonywania fundamentów. Do najechania pojazdem na zespoły wibracyjne zastosowano po cztery najazdy (w wersji krótkiej). Odmiany mobilne urządzeń są przeznaczone do kontroli skuteczności tłumienia zawieszenia pojazdu o dopuszczalnej masie całkowitej do 3,5 t. Urządzenia mogą być stosowane między innymi w stacjach kontroli pojazdów, stacjach obsługi samochodów oraz w warsztatach samochodowych (specjalizujących się w naprawie układów zawieszenia).
1. Urządzenia mobilne do badania zawieszenia
Niżej przedstawiono wybrane odmiany stanowisk z elektronicznymi układami pomiarowymi do kontroli skuteczności tłumienia zawieszenia pojazdu: Shocktester 3000 i 300 AFD firmy Boge/Sachs oraz TUZ-1 mobile wytwarzany przez firmę Unimetal. Są to urządzenia mobilne z najazdami.
1.1. Shocktester 3000 i 300 AFD firmy Boge/Sachs
Nieliczni wytwórcy oferują mobilne urządzenia do kontroli stanu technicznego układu zawieszenia. Na rys. 1 zamieszczono schemat i podstawowe wymiary wersji mobilnej stanowiska Shocktester 300 AFD. Natomiast na rys.2 przedstawiono ogólny widok urządzeń mobilnych Shocktester 3000 i 300 AFD firmy Boge/Sachs.
Podstawowe dane techniczne mobilnego urządzenia Shocktester 3000 zostały przedstawione w tabeli 1.
Wersja mobilna stanowiska Shocktester firmy Boge składa się z:
- dwóch zespołów wibracyjnych,
- czterech zespołów najazdowych,
- jednostki sterującej (pulpitu sterowniczego).
Zespoły wibracyjne należy ustawić na posadzce stanowiska. Do zespołów wibracyjnych mocowane są zespoły najazdowe. Zastosowano cztery jednakowe najazdy o wymiarach gabarytowych: długość 2190 mm, szerokość 500 mm, wysokość 276 mm. Zasada działania urządzenia mobilnego jest taka sama jak jego wersji stacjonarnej. Skuteczność tłumienia drgań w zawieszeniu pojazdu oceniana jest na podstawie analizy drgań w funkcji czasu (według testu Boge). Przebieg drgań jest rejestrowany przez czujniki indukcyjne przemieszczenia i po elektronicznym przetworzeniu przedstawiany na ekranie monitora lub na wyświetlaczach. Parametrem diagnostycznym jest podwójna amplituda drgań płyty najazdowej w strefie rezonansu, która jest porównywana z wartościami granicznymi wprowadzonymi do pamięci mikroprocesora. Ocenie podlega także różnica wartości podwójnych amplitud drgań między stroną lewą i prawą danej osi. Charakterystyki wzorcowe są systematycznie aktualizowane przez producenta i dostarczane na płytach CD (dyskietkach) użytkownikom urządzenia. Urządzenie jest wyposażone w drukarkę, która umożliwia otrzymanie protokołu z badań. Wyniki pomiarów rejestrowane są oddzielnie dla zawieszenia kół przednich i tylnych pojazdu. Protokół badania składa się z części liczbowej i graficznej.
1.2. TUZ-1 mobile firmy Unimetal
Charakterystyka techniczna mobilnego urządzenia do kontroli skuteczności tłumienia zawieszenia TUZ-1 mobile została przedstawiona w tabeli 2. Zasada działania urządzenia mobilnego jest taka sama jak jego wersji stacjonarnej. Skuteczność tłumienia drgań w zawieszeniu pojazdu ocenia się na podstawie analizy nacisku koła jezdnego na płytę stanowiska (według testu Eusama).
Mobilne urządzenie do kontroli skuteczności tłumienia drgań w układzie zawieszenia wytwarzane przez firmę Unimetal (rys. 3) składa się z:
- dwóch oddzielnych zespołów wibracyjnych,
- czterech zespołów najazdowych,
- dwóch podstaw zespołów najazdowych,
- jednostki sterującej (szafy sterowniczej).
Zespoły wibracyjne należy ustawić na posadzce stanowiska. Do zespołów wibracyjnych należy zamocować podstawy i zespoły najazdowe. Zastosowano cztery najazdy w wersji krótkiej (rys. 4) o następujących wymiarach gabarytowych: długość 1780 mm, szerokość 600 mm, wysokość 260 mm. Urządzenie TUZ-1 mobile powinno być zainstalowane w pomieszczeniu zamkniętym, ogrzewanym w okresie zimowym i posiadającym wyciąg spalin. Dopuszcza się czasowe usytuowanie urządzenia w okresie letnim na zewnątrz budynku (na powierzchni utwardzonej), po uprzednim zapewnieniu jego ochrony przed niekorzystnymi warunkami atmosferycznymi. Jednostkę sterującą (szafę sterowniczą) należy umieścić w miejscu zapewniającym dobrą widoczność i niestanowiącym przeszkody dla pojazdów, które będą przejeżdżać przez stanowisko. Zaleca się umieszczenie szafy sterowniczej po lewej stronie zespołów wibracyjnych. Odległość szafy sterowniczej od zespołów wibracyjnych w kierunku najazdu powinna wynosić około 3500 mm, natomiast w kierunku prostopadłym maksymalnie 1200 mm.
Mobilne stanowiska do badania układu zawieszenia pojazdu oferowane są również przez innych producentów. Przykładowo, na rys.5 przedstawiono odmianę takiego urządzenia wytwarzaną przez firmę Muller Bem/Monroe, która jest przystosowana do transportu przyczepą samochodową. Wymienione urządzenie znajduje się w ofercie firmy Acita.
2. Przyrządy do badania układów hydraulicznych
W przypadku pojazdu z zawieszeniem hydropneumatycznym do kontroli stanu technicznego układu hydraulicznego stosuje się następujące metody:
- diagnozowanie wstępne,
- badanie stanu oleju hydraulicznego,
- pomiar parametrów diagnostycznych.
Diagnozowanie wstępne instalacji hydraulicznych najczęściej obejmuje: zewnętrzne sprawdzenie elementów i zespołów układu hydraulicznego, ocenę szczelności oraz próbę działania. Stan oleju może być badany metodami uproszczonymi, w pobliżu obiektu, za pomocą przenośnych zestawów diagnostycznych, które z reguły umożliwiają sprawdzenie lepkości kinematycznej, czystości, kwasowości i zawartości wody w oleju. Natomiast metodami przyrządowymi mierzy się parametry diagnostyczne określające stan techniczny układów hydraulicznych. Najczęściej dokonuje się pomiaru: ciśnienia, szczelności, wydatku, temperatury, prędkości obrotowej, przecieków wewnętrznych i parametrów geometrycznych. Podczas badania zespołów hydraulicznych na ogół wykonuje się równoczesny pomiar kilku parametrów diagnostycznych. Podczas pomiaru parametrów diagnostycznych układu hydraulicznego niezbędna jest dobra znajomość jego budowy i działania. Umożliwia to prawidłowy wybór punktów diagnostycznych, ustalenie wartości mierzonych parametrów w wybranym punkcie oraz interpretację otrzymanych wyników pomiaru.
Przyrządy do oceny stanu technicznego układu hydraulicznego można podzielić na dwie grupy:
- manometry (z wyposażeniem pomocniczym), umożliwiające pomiar chwilowej wartości ciśnienia cieczy w wybranym punkcie układu oraz ocenę szczelności (przez pomiar spadku ciśnienia w określonym czasie);
- przenośne przyrządy, umożliwiające całościowe badanie instalacji hydraulicznych.
Stosowanie manometrów do diagnozowania instalacji hydraulicznych jest celowe zwłaszcza w przypadku wykonywania prostych pomiarów w układach hydrauliczno-mechanicznych. Najczęściej używa się manometrów o zakresie pomiarowym 0¸16 MPa z wyposażeniem pomocniczym (trójnik, przewód elastyczny ze złączami gwintowymi, komplet złączy redukcyjnych). Do pomiaru objętościowego natężenia przepływu (wydatku) oleju w instalacjach hydraulicznych używa się różnego typu przepływomierzy, na przykład turbinowych i suwakowych. Przykładem takich testerów mogą być przyrządy produkcji krajowej USDH-3A (turbinowy) oraz HT-3SM (suwakowy) przeznaczone do diagnozowania instalacji hydraulicznych. Po odpowiednim podłączeniu mogą być używane do diagnozowania zespołów układu hydraulicznego samochodu (także zawieszenia hydropneumatycznego). Charakterystykę techniczną wymienionych przepływomierzy zestawiono w tabeli 3.
Przepływomierz turbinowy USDH-3A umożliwia pomiar wydatku pompy, ciśnienia roboczego, temperatury oleju, prędkości obrotowej pompy (wału korbowego silnika), spadku ciśnienia w określonym czasie (szczelności). Na rys. 6 przedstawiono schemat układu pomiarowego tego przyrządu:
Wewnątrz urządzenia możliwe są dwa obiegi oleju:
- I obieg – olej od pompy hydraulicznej jest doprowadzany do złącza dolotowego (10), dalej przez przepływomierz (6) do zaworu dławiącego (5) i złącza zlewowego (11), które łączy się ze zbiornikiem; obieg ten jest stosowany podczas pomiaru wydatku oleju;
- II obieg – po otwarciu zaworu odcinającego (7) włącza się drugi obwód, ciśnieniowe złącze wylotowe (12) łączy się z zespołem, w którym dokonuje się pomiaru ciśnienia (np. ciśnienia otwarcia zaworu bezpieczeństwa) lub badania nieszczelności wewnętrznych (np. w siłowniku).
Możliwości pomiarowe przepływomierza USDH-3A pozwalają na ocenę stanu technicznego układów hydraulicznych zarówno w pojazdach samochodowych, jak i w maszynach roboczych. Z praktyki diagnostycznej wynika, że przepływomierze turbinowe są wrażliwe na zanieczyszczenia oleju i na wstrząsy. W związku z tym występuje konieczność częstego demontażu, kontroli i ewentualnego czyszczenia wirnika i jego łożysk. Zanieczyszczenia można ograniczyć stosując na wlocie do przepływomierza dodatkowy filtr o dokładności filtrowania co najmniej 16 mm. Podczas diagnozowania układów hydraulicznych zakłada się, że przepływomierz powinien mieć klasę dokładności nie większą niż 2,5. Dokładność pomiaru przepływomierzy turbinowych w dolnej części zakresu pomiarowego jest niewielka, a w pozostałej części w dużym stopniu zależy od lepkości kinematycznej oleju. Aby uniknąć błędów wynikających z zakłóceń pola magnetycznego, przepływomierze turbinowe powinny być umieszczone w pewnej odległości od pracujących maszyn elektrycznych (silników, prądnic, alternatorów). Znanym wytwórcą przyrządów do badania instalacji hydraulicznych jest firma Hydac. Na rys.7 przedstawiono przyrząd HMG 2020 tej firmy (z wyposażeniem), który jest przeznaczony do wykonywania bieżących pomiarów diagnostycznych w układach hydraulicznych. Jest to przyrząd uniwersalny, którym można wykonywać równoczesne pomiary kilku wielkości fizycznych. Można przeprowadzać zarówno pomiar ciągły parametrów diagnostycznych, jak i pomiar wartości szczytowych i różnic wskazań.
Urządzenie HMG 2020 przeznaczone jest do pomiaru wartości ciśnienia, temperatury, natężenia przepływu, prędkości obrotowej i innych parametrów diagnostycznych. Do współpracy z przyrządem służą następujące przetworniki:
- ciśnienia o klasach dokładności: 0,3%, 0,5% i 1% oraz zakresie ciśnienia do 60 MPa,
- temperatury ETS 4000 o zakresie pomiarowym od – 25OC do +100OC,
- przepływu (turbinowe) o następujących zakresach pomiarowych: 6-60 dm3/min, 15÷300 dm3/min i 40÷600 dm3/min,
- sonda HDS 1000 do pomiaru prędkości obrotowej (np. wału silnika napędzającego pompę hydrauliczną),
- kryza do pomiaru natężenia przepływu o następujących zakresach: 5÷20 dm3/min, 20÷80 dm3/min i 80÷350 dm3/min.
Dane pomiarowe mogą być zapamiętane i wydrukowane w postaci graficznej lub liczbowej w protokole z badań. Wydruk można wykonać na standardowych drukarkach dostępnych na rynku. Z urządzeniem współpracuje wiele dodatkowego oprzyrządowania oraz pakiet oprogramowania HMGDESK przeznaczony do współpracy z komputerem osobistym PC, rozszerzający możliwości pomiarowe.
Osprzęt do przyrządu HMG oferowany przez firmę Hydac obejmuje między innymi: oprogramowanie do komputera osobistego, przetworniki ciśnienia, temperatury oraz wydatku, sondę do pomiaru prędkości obrotowej, drukarkę atramentową, przewody przyłączeniowe i złącza adaptacyjne.
3. Algorytm kontroli stanu i lokalizacji uszkodzeń
Praktyczna realizacja procesu diagnostycznego pojazdu samochodowego wymaga znajomości i posiadania:
- metod diagnozowania,
- przyrządów (urządzeń, środków) diagnostycznych,
- algorytmów kontroli stanu i lokalizacji uszkodzeń.
Rozróżnia się dwie fazy badań i oceny stanu pojazdu samochodowego (układu, zespołu):
- kontrolę stanu,
- lokalizację uszkodzeń.
Zadaniem najbardziej ogólnym w procesie diagnozowania samochodu lub jego układu (mechanizmu) jest określenie stanu obiektu w całości, bez rozróżniania jego elementów. Celem badania jest stwierdzenie, czy obiekt jako całość nadaje się do użytku. Takie badanie nazywa się kontrolą stanu samochodu lub jego układu (zespołu). Uzyskanie przynajmniej jednego negatywnego wyniku sprawdzenia oznacza, że pojazd (układ) znajduje się w stanie niezdatności i powinien być skierowany do drugiej fazy badań, to jest ustalenia stanu elementów pojazdu (układu) celem ich regulacji, naprawy lub wymiany. Takie badanie nazywa się lokalizacją uszkodzeń. Do realizacji kontroli stanu i lokalizacji uszkodzeń służą algorytmy. Algorytm kontroli stanu i (lub) lokalizacji uszkodzeń jest to uporządkowany minimalny zbiór sprawdzeń diagnostycznych. Natomiast sprawdzenie to pomiar i ustalenie wartości parametru diagnostycznego.
Niżej przedstawiono przykładowy algorytm kontroli stanu i lokalizacji uszkodzeń układu zawieszenia.
dr inż. Kazimierz Sitek
Komentarze (0)