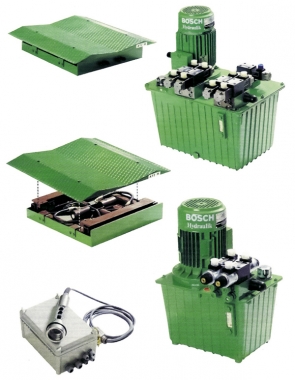
W praktyce najczęściej stosuje się badanie amortyzatorów w stanie zamontowanym w pojeździe, z uwagi na łatwość i szybkość wykonania pomiaru. Spośród dwóch dostępnych metod badania układu zawieszenia, tj. metody drgań swobodnych i metody drgań wymuszonych, ta druga znalazła powszechne zastosowanie do określania stanu technicznego zawieszenia samochodu. Aktualnie produkowane urządzenia do badania układu zawieszenia metodą drgań wymuszonych wykonywane są w wersji stacjonarnej lub mobilnej (z rampami najazdowymi). Mogą być stosowane do kontroli zawieszenia tylko w samochodach osobowych, osobowo-terenowych i dostawczych. Diagnozowanie układu zawieszenia samochodów ciężarowych, autobusów, przyczep oraz naczep nadal jest wykonywane metodami organoleptycznymi.
Do diagnozowania układu zawieszenia pojazdów samochodowych obecnie stosuje się następujące rodzaje urządzeń:
- przyrządy do sprawdzania luzów,
- urządzenia do badania zawieszenia (amortyzatorów) metodą drgań swobodnych,
- urządzenia do badania zawieszenia (amortyzatorów) metodą drgań wymuszonych,
- przyrządy do sprawdzania instalacji hydraulicznych.
1. Przyrządy do sprawdzania luzów
Podczas określania stanu technicznego pojazdu samochodowego istotną rolę odgrywa umiejętność oceny luzów w podstawowych układach i mechanizmach pojazdu. Za dopuszczalne uznaje się luzy nieznaczne, widoczne dopiero po bardzo uważnych oględzinach. Nadmierne luzy są łatwo zauważalne, wyraźnie wyczuwalne na styku płaszczyzn łączonych elementów. Nadmiernym luzom często towarzyszy stuk, a zawsze opóźnienie ruchu zespołu spowodowane jest koniecznością likwidacji luzu w połączeniu. Wyczuwalne luzy świadczą o usterkach lub nadmiernym, niedopuszczalnym zużyciu jednego lub kilku elementów w kontrolowanych układach i mechanizmach pojazdu. Do ułatwienia oceny luzów w układach zawieszenia, kierowniczym i jezdnym wykorzystuje się specjalne urządzenia wymuszające szarpanie badanych połączeń. Urządzenia te, nazywane detektorami luzów lub szarpakami, składają się z dwóch napędzanych siłownikami hydraulicznymi lub pneumatycznymi płyt, na których są stawiane koła pojazdu. Płyty te wykonują krótkie przemieszczenia (obroty) w różnych kierunkach i powodują poziome ruchy koła oraz wszystkich elementów z nim związanych.
Ze względu na przeznaczenie rozróżnia się urządzenia do wymuszania szarpnięć kołami jezdnymi:
- w pojazdach o dmc do 3,5 t,
- w pojazdach o dmc powyżej 3,5 t,
- uniwersalne.
Ze względu na rodzaj napędu stosowane są urządzenia z napędem hydraulicznym lub z napędem pneumatycznym. W przypadku testerów do badania luzów w pojazdach o dmc do 3,5 t najczęściej stosuje się pneumatyczne zasilanie robocze. Natomiast w urządzeniach uniwersalnych i przeznaczonych do kontroli pojazdów o dmc ponad 3,5 t na ogół występuje zasilanie hydrauliczne (większa płynność ruchu, mniejsze wymiary elementów).
Urządzenia szarpiące składają się z następujących zasadniczych zespołów (rys. 1):
- zespoły płyt do wymuszania szarpnięć kołami (działające niezależnie),
- zespół zasilający,
- zespół sterujący,
- przyrząd do blokowania pedału hamulca.
Oddzielny zespół zasilający nie występuje w przypadku urządzeń z napędem pneumatycznym, które są zasilane z sieci sprężonego powietrza oraz urządzeń instalowanych na podnośnikach – wykorzystuje się układ zasilania podnośnika.
W tego typu urządzeniach istotne jest sterowanie oraz koordynacja ruchu płyt. Za optymalną najczęściej przyjmuje się następującą kombinację ruchów płyt szarpiących (rys. 2):
- ruch skrętny i ruch w kierunku poprzecznym (dla urządzeń do wymuszania szarpnięć kołami w pojazdach o dmc do 3,5 t),
- ruch w kierunku wzdłużnym i w kierunku poprzecznym (dla urządzeń do wymuszania szarpnięć kołami w pojazdach o dmc powyżej 3,5 t).
Sterowanie ruchami płyt realizowane jest przewodowo lub bezprzewodowo pilotem wbudowanym w korpus ręcznej lampy halogenowej, która służy jednocześnie do oświetlania kontrolowanych węzłów. Urządzenia szarpiące umożliwiają organoleptyczną kontrolę luzów w niżej wymienionych elementach (węzłach) układów podwozia samochodu:
- sworznie zwrotnicy,
- łożyska piast kół,
- wahacze,
- drążki kierownicze,
- stabilizatory,
- przeguby.
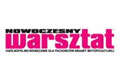
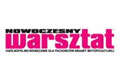
W celu zapewnienia uniwersalności stanowiska wprowadzono dwa zakresy skoku płyt najazdowych (±30 mm i ±50 mm). Siła wymuszająca ruch płyt wynosi 30 kN, maksymalny nacisk osi 160 kN, a ciśnienie robocze 15,2 MPa. Kontrolę luzów przeprowadza się po najechaniu kołami pojazdu na przesuwne płyty szarpiące przez wymuszanie ruchu koła jezdnego w kierunku wzdłużnym i poprzecznym, z jednoczesną obserwacją sprawdzanych elementów zawieszenia, układu kierowniczego i jezdnego oświetlanych silnym strumieniem światła halogenowej lampy sterującej. Przebieg kontroli obejmuje czynności związane z ustawieniem samochodu, pracą na urządzeniu i zakończeniem pracy. Urządzenie może stanowić indywidualne stanowisko kontroli pojazdów lub zostać włączone w zestaw linii diagnostycznej. Przystosowane jest do zabudowania z lewej i prawej strony kanału przeglądowego. Jest obsługiwane jednoosobowo przez przeszkolonego diagnostę. Detektor luzów z napędem pneumatycznym SZ-3.5 firmy Unimetal umożliwia wymuszanie szarpnięć kołami jezdnymi pojazdu o dopuszczalnej masie całkowitej do 3,5 t. Urządzenie pełni funkcję pomocniczą podczas oceny luzów w przegubach, sworzniach, łożyskach i końcówkach drążków kierowniczych.
Schemat blokowy detektora luzów SZ-3.5 przedstawiono na rys. 7. Urządzenie składa się z następujących zasadniczych elementów: dwóch zespołów szarpaków – platforma prawa i lewa (rys. 8), szafki sterującej i lampy sterującej (rys. 9) oraz przyrządu do blokowania wciśniętego pedału hamulca. Zespół szarpaka zbudowany jest z:
- korpusu platformy,
- płyty szarpiącej (roboczej),
- ramy pośredniej z wkładkami ślizgowymi,
- zespołu siłowników pneumatycznych z układem dźwigniowym,
- instalacji pneumatycznej,
- instalacji elektrycznej.
Korpus platformy jest przymocowany do fundamentu stanowiska. Płyty szarpiące zamocowane są suwliwie na prowadnicach nośnych oraz połączone przez układ dźwigni z tłoczyskami siłowników pneumatycznych w sposób umożliwiający otrzymywanie ruchów poprzecznych i skrętnych. Pokrywa płyt pokryta jest specjalną powłoką o dużej twardości i wysokim współczynniku tarcia. Układ dźwigniowy z siłownikami pneumatycznymi zainstalowany jest w korpusie platformy. Dźwignia powodująca ruch poprzeczny płyty szarpiącej połączona jest jednym ramieniem z tłoczyskiem siłownika, natomiast drugie ramię połączone jest z płytą szarpiącą za pomocą dźwigni pośredniej. Dźwignia powodująca ruch skrętny płyty szarpiącej połączona jest jednym końcem z tłoczyskiem siłownika, natomiast drugi koniec połączony jest przez dźwignię z ramą pośrednią znajdującą się pod płytą.
Instalacja pneumatyczna urządzenia zasilana jest przez zawór odcinający z sieci sprężonego powietrza o ciśnieniu 0,6÷0,8 MPa. Sprężone powietrze dostarczane jest do zaworów rozdzielających, które na przemian doprowadzają je do jednej lub drugiej komory siłowników, powodując przemieszczanie tłoczyska i ruch płyt szarpiących. W elementach pneumatycznych zastosowano wysokiej jakości uszczelnienia oraz skuteczne tłumiki hałasu. Instalacja elektryczna urządzenia jest podłączona do zasilacza 230/24/12 V umieszczonego w szafce sterującej. Do sterowania zaworów rozdzielających stosuje się napięcie 24 V, natomiast do zasilania halogenowej lampy sterującej napięcie 12 V. W szafce sterującej umieszczone są elementy układu zasilania: transformatory, przekaźniki oraz bezpieczniki. Lekka, trwała i ergonomiczna lampa sterująca służy do sterowania urządzeniem szarpiącym i stanowi jego integralną część. Podłączona jest do szafki sterującej. W korpusie wbudowane są przyciski sterujące oraz latarka halogenowa. Lampa sterująca umożliwia ręczne sterowanie urządzeniem i jednoczesną obserwację elementów podwozia przez obsługującego. Sterownik zapewnia ruch poprzeczny lub ruch skrętny płyty szarpiącej, każdego zespołu osobno albo obu płyt jednocześnie. Przy ruchu jednoczesnym w kierunku poprzecznym zwroty przesuwu obu płyt są przeciwne, przy ruchu skrętnym obie płyty obracają się w prawo.
Sterowanie lampą można podzielić na dwa etapy:
- wybór napędu płyt szarpiących (strona lewa, strona prawa, dwie strony),
- włączenie ruchów roboczych (poprzecznego lub skrętnego).
Po wciśnięciu na lampie sterującej przycisku włączającego żarówkę oświetlającą, staje się możliwa obserwacja elementów układów: zawieszenia, kierowniczego i jezdnego podczas oceny luzów.
Włączenie zasilania sygnalizuje lampka kontrolna umieszczona na ścianie czołowej szafki sterującej. Przygotowanie urządzenia do pracy obejmuje sprawdzenie szczelności połączeń układu pneumatycznego i poprawności funkcjonowania przycisków lampy sterującej. Obsługa urządzenia jest bardzo prosta, dostosowana do manualnych możliwości człowieka.
2. Urządzenia do badania zawieszenia metodą drgań swobodnych
Charakterystyki amplitudowe zanikających drgań nadwozia na jego zawieszeniu (tzw. drgań swobodnych) można uzyskać następującymi sposobami:
- przez gwałtowne opuszczanie badanej osi samochodu,
- przez wychylenie nadwozia z położenia równowagi w wyniku ugięcia elementów sprężystych (np. przyrząd Big Red firmy M-Tronic),
- na stanowisku płytowym, które umożliwia wykorzystanie wymuszenia niskoczęstotliwościowego występującgo w czasie hamowania (np. urządzenie Univers A2 i A4 firmy Heka).
W pierwszym przypadku najeżdża się kołami na przykład na podstawki w kształcie klina, z których koła spadają swobodnie i wzbudzają drgania nadwozia na zawieszeniu, rejestrowane przez urządzenie pomiarowe. Wysokość spadania dobiera się tak, aby nie nastąpiło uderzenie o ograniczniki. Stan amortyzatorów ocenia się na podstawie liczby i amplitudy drgań. Uzyskane wyniki porównuje się z odpowiednimi wykresami wzorcowymi. W tym sposobie występują trudności uzyskania jednakowych wartości amplitudy początkowej. Do tej metody można również wykorzystać urządzenie zwalniające zapadnię (np. FWT 2000 firmy Cartec), to jest podstawkę, płytę najazdową lub ramę (w zależności od rozwiązania konstrukcyjnego). Samochód wjeżdża na platformy kołami przednimi lub tylnymi. Po opuszczeniu pojazdu rejestrowane są zanikające drgania swobodne charakteryzujące tłumienie amortyzatorów. Drugi sposób pomiaru, polegający na wychyleniu nadwozia z położenia równowagi, zastosowano w testerach SDT 2000/U oraz Big Red firmy M-Tronic (rys. 10). Są to przyrządy przenośne, o niewielkich gabarytach, wyposażone we własne źródło zasilania. Ich zastosowanie nie wymaga specjalnie przygotowanego stanowiska. Tester (czujnik ultradźwiękowy) przymocowany do nadwozia odbiera sygnały odbite od nadajnika sygnałów umieszczonego na podłożu i przekazuje je do opracowania przez mikroprocesor. Do obsługi przyrządu służą przyciski umieszczone na jego ścianie czołowej. Podczas kontroli nie ma potrzeby wprowadzania do pamięci przyrządu kryteriów oceny stanu zawieszenia badanego samochodu. Dane te zostały wprowadzone do oprogramowania testera. Uwzględniono przy tym występujące w praktyce trzy rodzaje charakterystyk tłumienia zawieszeń: normalne, sportowe i miękkie. Po wybraniu rodzaju zawieszenia otrzymamy wynik pomiaru w postaci odpowiednich symboli z dodatkowymi informacjami. Znaczenie poszczególnych symboli graficznych jest następujące:
- znak w postaci słupka oznacza, że są spełnione wymagania przyjęte dla tej kategorii zawieszenia (wysokość słupka świadczy o jakości tłumienia drgań),
- znak w postaci trójkąta ostrzegawczego świadczy o tym, że nie są spełnione wymagania przyjęte dla danego rodzaju zawieszenia,
- znak STOP oznacza, że nie są spełnione minimalne wymagania związane z bezpieczeństwem jazdy dla żadnej z kategorii zawieszeń.
Do określenia tłumienia drgań nadwozia nie jest potrzebne kalibrowanie przyrządu pomiarowego (wynik pomiaru nie zależy od siły naciśnięcia na błotnik podczas uginania nadwozia). Zastosowane oprogramowanie pozwala także na wybranie z menu funkcji umożliwiającej pomiar własnych wartości granicznych parametrów diagnostycznych (kryteriów oceny stanu zawieszenia) i wprowadzenie ich do pamięci w postaci wzorca dla kolejnych pomiarów.
Badany samochód należy ustawić na płaskim podłożu. Tester powinno się zamocować do błotnika nad badanym kołem za pomocą przyssawek (rys. 11). Następnie na posadzce przy kole kładzie się nadajnik ultradźwięków i łączy go przewodem z przyrządem. Po wykonaniu czynności przygotowawczych należy krótko i silnie nacisnąć na błotnik, co spowoduje ugięcie zawieszenia. Czujniki ultradźwiękowe znajdujące się w dolnej części przyrządu rejestrują sygnały odbite od nadajnika. Wewnętrzny mikroprocesor testera oblicza dane niezbędne do oceny stanu zawieszenia pojazdu. Następnie przestawia się przyrząd nad kolejne koła i wykonuje identyczne czynności. Rzeczywisty przebieg drgań swobodnych nadwozia oraz liczbową i słowną ocenę sprawności amortyzatorów otrzymuje się na wyświetlaczu ciekłokrystalicznym przyrządu. Tester jest również wyposażony w drukarkę termiczną. Na wydruku jest podawana tekstem oraz w formie graficznej ocena stanu technicznego amortyzatorów. Otrzymuje się jedną z trzech możliwych informacji o ich skuteczności działania. Na rys. 12 przedstawiono przykładowy wydruk wyników pomiaru amortyzatorów przyrządem Big Red.
Firma Heka proponuje trzeci sposób sprawdzania amortyzatorów metodą drgań swobodnych – na urządzeniach płytowych Univers A2 i A4 do badania hamulców oraz zawieszenia. Skuteczność tłumienia poszczególnych amortyzatorów jest badana po pełnym wyhamowaniu samochodu na stanowisku, gdy następuje ich maksymalne ugięcie jako reakcja od sił hamowania, a następnie zanikanie ugięć, aż do osiągnięcia stanu równowagi. Wykorzystanie do badania amortyzatorów wymuszenia niskoczęstotliwościowego, występującego w trakcie hamowania, nie znalazło szerszego zastosowania ze względu na niewielką dokładność i małą powtarzalność uzyskanych wyników (potwierdzają to badania wykonane metodami symulacyjnymi).
dr inż. Kazimierz Sitek
Literatura artykułu dostępna w redakcji.
Komentarze (0)