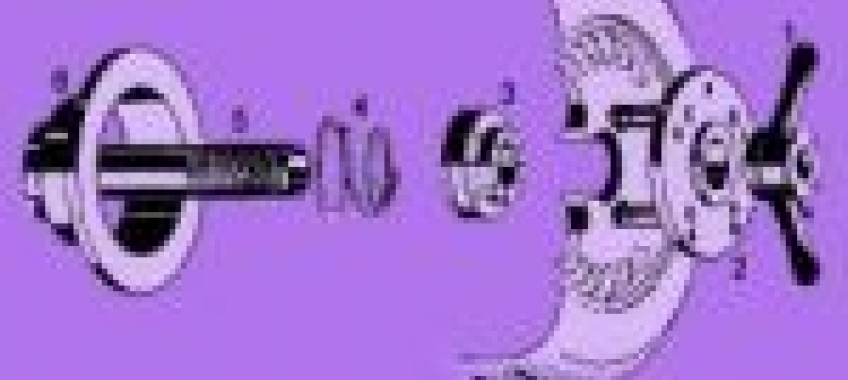
Do oceny stanu technicznego układu jezdnego stosuje się następujące przyrządy i urządzenia:
- przyrządy do wykrywania luzów,
- urządzenia do wykrywania uszkodzeń wewnętrznych opon,
- przyrządy do pomiaru bicia obręczy i opony,
- przystawki napędowe do wykrywania niewyrównoważenia kół nienapędzanych,
- wyważarki do kół jezdnych,
- linie do obsługiwania i diagnozowania kół.
1. Przyrządy do wykrywania luzów
Sprawdzanie luzów w elementach układu jezdnego, układu zawieszenia i układu kierowniczego umożliwiają urządzenia do wymuszania szarpnięć kołami jezdnymi pojazdu. Są to urządzenia płytowe, montowane w posadzce na obrzeżach kanału przeglądowego (rys. 1) lub na podnośniku, napędzane siłownikami hydraulicznymi lub pneumatycznymi, zdalnie sterowane specjalnymi przyciskami umieszczonymi w ręcznej lampie halogenowej. Płyty, po najechaniu na nie kołami danej osi, wykonują krótkie przemieszczenia (obroty) w różnych kierunkach, powodując poziome ruchy koła i wszystkich elementów z nim związanych.
Ze względu na przeznaczenie rozróżnia się urządzenia do wymuszania szarpnięć kołami jezdnymi (detektory luzów):
- w pojazdach o dmc do 3,5 t,
- w pojazdach o dmc powyżej 3,5 t,
- uniwersalne.
Rys. 1. Urządzenie szarpiące AM 800 K z napędem hydraulicznym (źródło: Josam): a – elementy składowe, b – rozmieszczenie na obrzeżach kanału przeglądowego.
W tabeli 1 przykładowo przedstawiono podstawowe dane techniczne urządzeń szarpiących (wersje osobowa i uniwersalna) wytwarzanych przez firmę Unimetal. Ze względu na rodzaj napędu występują urządzenia z napędem hydraulicznym lub z napędem pneumatycznym. W przypadku testerów do badania luzów w pojazdach o dmc do 3,5 t najczęściej stosuje się pneumatyczne zasilanie robocze. Natomiast w urządzeniach uniwersalnych i przeznaczonych do kontroli pojazdów o dmc ponad 3,5 t na ogół występuje zasilanie hydrauliczne (większa płynność ruchu, mniejsze wymiary elementów).
Urządzenie szarpiące składa się z następujących zasadniczych zespołów (rys. 2):
- niezależnie funkcjonujące zespoły płyt do wymuszania szarpnięć kołami,
- zespół zasilający,
- zespół sterujący,
- przyrząd do blokowania pedału hamulca.
Oddzielny zespół zasilający nie występuje w przypadku urządzeń z napędem pneumatycznym (zasilanych z sieci sprężonego powietrza) oraz urządzeń instalowanych na podnośnikach – wykorzystuje się układ zasilania podnośnika.
W tego typu urządzeniach istotne jest sterowanie i koordynacja ruchu płyt. Każdy zespół płyty powinien umożliwiać następujące ruchy koła jezdnego:
- ruch skrętny i ruch w kierunku poprzecznym, dla urządzeń do wymuszania szarpnięć kołami w pojazdach o dmc do 3,5 t,
- ruch w kierunku wzdłużnym i w kierunku poprzecznym, dla urządzeń do wymuszania szarpnięć kołami w pojazdach o dmc powyżej 3,5 t.
Sterowanie ruchami płyt realizowane jest przewodowo lub bezprzewodowo pilotem wbudowanym w korpus ręcznej lampy halogenowej, która służy jednocześnie do oświetlania kontrolowanych węzłów.
Analiza danych technicznych urządzeń szarpiących różnych producentów wskazuje, że podstawowe parametry techniczne stosowanych odmian tych urządzeń są porównywalne (np. dopuszczalny nacisk osi, siła wymuszająca ruch płyt, skok płyty szarpiącej). Urządzenia montuje się na płytach najazdowych podnośnika nożycowego albo 4-kolumnowego (rys. 3) lub w posadzce stanowiska na obrzeżach kanału przeglądowego. Detektory luzów są wytwarzane przez różnych producentów, na przykład: Cartec, Cemb, Fudim-Polmo, Hofmann, Josam, Maha, Tecnotest, Unimetal.
Rys. 2. Elementy urządzenia szarpiącego SZ-3.5 z napędem pneumatycznym (źródło: Unimetal).
Rys. 3. Detektor luzów umieszczony na płytach najazdowych podnośnika (źródło: Car-Lift).
2. Urządzenia do wykrywania uszkodzeń wewnętrznych opon
Stopień zużycia ogumienia ma bardzo duży wpływ na bezpieczeństwo jazdy. Decydują o tym m.in. głębokość rzeźby bieżnika, liczba, wymiary i rozmieszczenie uszkodzeń na obwodzie, charakter zużycia bieżnika, rozwarstwienia lub pęknięcia naruszające osnowę. Niektóre uszkodzenia ogumienia nie są widoczne z zewnątrz i nie można ich wykryć metodami organoleptycznymi (np. rozwarstwienie elementów osnowy, przecięcie lub naderwanie włókien osnowy oraz opasania). Firma Beissbarth opracowała oryginalne urządzenie do badania opon mtt 2100 (rys.4a), które wykrywa uszkodzenia wewnętrzne opon bezpośrednio na samochodzie. Urządzenie działa w połączeniu z rolkowym stanowiskiem do sprawdzania hamulców.
Urządzenie do wykrywania uszkodzeń opon składa się z:
- głowic pomiarowych wyposażonych w laserowe źródła światła, kamer CCD ze specjalnym układem optycznym i układu sterująco-zasilającego,
- układu mechanicznego służącego do ustawiania głowic pomiarowych w wybranym położeniu (przegubowe ramię) oraz sterowanej pneumatycznie blokady położenia głowic,
- jednostki komputerowej z kolorowym monitorem i klawiaturą poszerzonej o kartę PCI do rejestracji zdjęć i obróbki obrazu.
Rys. 4. Urządzenie mtt 2100 firmy Beissbarth do wykrywania wad wewnętrznych ogumienia zespolone z urządzeniem rolkowym do badania hamulców (a) oraz przykładowy widok ekranu po wykonaniu badania ogumienia (b).
Po wjechaniu kołami jednej osi na rolki, następuje sprawdzenie hamulców. Następnie osoba obsługująca przyłącza do sprawdzanych kół przewody ze sprężonym powietrzem i zbliża do nich głowice pomiarowe. Przegubowe ramię i laserowy system pozycjonujący umożliwia ustawienie ich na wysokości osi kół, w niewielkiej odległości od nich. Po ustawieniu głowic można rozpocząć wyszukiwanie uszkodzeń wewnętrznych opon. Sterowany komputerowo układ pomiarowy dzieli obwód opony na 7 do 9 segmentów, aby każdy z nich sprawdzić oddzielnie. Rolki do kontroli hamulców służą jedynie do obrotu kół o określony kąt, tak by kolejne segmenty opon ustawiły się naprzeciw obiektywu kamer CCD umieszczonych w głowicach pomiarowych. Dla poszczególnych segmentów opony, wyszukiwanie uszkodzeń wewnętrznych odbywa się w następujący sposób:
- w oponie jest ustalane w sposób automatyczny określone ciśnienie,
- kamera CCD wykonuje pierwsze zdjęcie wybranego segmentu opony, oświetlonego światłem laserowym,
- ciśnienie w oponie zostaje automatycznie obniżone o określoną wartość,
- kamera CCD wykonuje drugie zdjęcie tego samego segmentu opony,
- uzyskane zdjęcia są porównywane komputerowo i analizowana jest zmiana kształtu zewnętrznej powłoki opony (zmiany długości fragmentów powłoki opony). Następnie wyniki badania opon są przedstawiane na ekranie komputerowym (rys. 4b). Po lewej stronie widoczna jest opona, której obwód został podzielony na segmenty, a po prawej powiększenie wybranego segmentu. Oznaczane są miejsca uszkodzenia opony. Program dokonuje oceny czy opona może być dopuszczona do dalszej eksploatacji. Wynik kontroli można uzyskać również w postaci wydruku. Urządzenie umożliwia sprawdzanie ogumienia bezpośrednio na pojeździe. Uzyskuje się jednoznaczną ocenę zarówno widocznych, jak i ukrytych uszkodzeń opon. Badanie może być włączone w program przeglądu technicznego samochodu na stacji kontroli pojazdów. Znane są również inne rozwiązania urządzeń do badania uszkodzeń ogumienia, które umożliwiają wykrywanie uszkodzeń opon po wymontowaniu koła z samochodu i zamontowaniu go na wale napędowym urządzenia. Sposób wyszukiwania uszkodzeń jest identyczny do opisanego wyżej. Sprawdzenie jednej opony trwa około 1,5 min. Ten rodzaj urządzeń do badania wad wewnętrznych opon jest wytwarzany m.in. przez firmy Beissbarth i Maha (rys. 5).
Rys. 5. Urządzenie RDT-S1 do badania wad wewnętrznych opon kół wymontowanych z pojazdu (źródło: Maha).
3. Przyrządy do pomiaru bicia obręczy i opony
Przed kontrolą wyrównoważenia koła należy sprawdzić promieniowe i osiowe bicie obręczy i opony. Do pomiaru bicia stosuje się rysik na podstawce lub specjalne przyrządy z czujnikiem zegarowym (rys. 6). W celu zmierzenia bicia opony należy koło podnieść, a do opony dosunąć rolkę przyrządu. Podczas pomiaru bicia promieniowego rolka powinna być dostawiona do czoła opony w płaszczyźnie symetrii koła, a podczas pomiaru bicia osiowego - do boku opony w płaszczyźnie poziomej przechodzącej przez oś koła. Koło obracać ręką i zaobserwować maksymalne i minimalne wychylenia wskazówki czujnika. Różnica tych wychyleń jest wartością bicia opony. W podobny sposób mierzy się bicie obręczy. Pomiar bicia koła można również wykonać czujnikiem, który wchodzi w skład wyposażenia niektórych wyważarek stacjonarnych. Najnowsze generacje wyważarek komputerowych bicie (promieniowe i osiowe) obręczy oraz opony mierzą w sposób automatyczny i wyniki tego pomiaru uwzględniają w procesie wyrównoważania kół jezdnych.
Rys. 6. Przyrząd do pomiaru bicia koła jezdnego: 1 – czujnik zegarowy z końcówką rolkową, 2 – wspornik z zaciskiem, 3 – trzpień, 4 – podstawka.
4. Przystawki napędowe do wykrywania niewyrównoważenia kół
Niewyrównoważenie kół nienapędzanych można wykryć za pomocą przystawki napędowej, na przykład RK-1 firmy Unimetal przedstawionej na rys.7. W tym celu należy unieść przód samochodu i przystawić do czoła opony rolkę napędową przyrządu obracającą się z maksymalną prędkością. Po odsunięciu przystawki, w przypadku niewyrównoważenia koła samochodu, można zaobserwować drgania tego koła oraz całego nadwozia. Niewyrównoważenie kół napędowych można wykryć po podniesieniu osi napędzanej, uruchomieniu silnika i włączeniu biegu bezpośredniego. Jeżeli koła są niewyrównoważone, to przy większych prędkościach wystąpią ich drgania przenoszące się na nadwozie. Przystawki napędowe wykonywane są również w postaci urządzeń do napędzania koła i są wówczas jednym z elementów składowych wyważarek dostawnych. Przykład takiego rozwiązania pokazano na rys.8.
Rys. 7. Przystawka napędowa RK-1 do rozpędzania kół jezdnych samochodów osobowych i dostawczych (źródło: Unimetal).
Rys.8 . Urządzenie do napędzania koła jezdnego – element składowy wyważarki dostawnej Microtec 600 (źródło: Beissbarth).
Przystawki napędowe mają silnik elektryczny o mocy około 2 kW i prędkości obrotowej 1200÷1300 obr./min, wyposażony w rolkę napędową osadzoną bezpośrednio na wale silnika. Prędkość obwodowa rolki napędowej wynosi 90÷120 km/h.
5. Urządzenia do wyrównoważania kół (wyważarki)
Wyrównoważanie kół jezdnych powinno się przeprowadzić w przypadku:
- drgań koła kierownicy lub nadwozia,
- nierównomiernego zużycia bieżnika opon,
- wymiany opon,
- naprawy ogumienia,
- uszkodzenia koła.
Wyrównoważanie kół przeprowadza się za pomocą specjalnych urządzeń zwanych wyważarkami. Urządzenia te pozwalają na określenie kątowej lokalizacji niewyrównoważenia, jak również na określenie wartości tego niewyrównoważenia.
1) Klasyfikacja wyważarek
Ze względu na sposób wyrównoważenia kół wyważarki dzieli się na:
- stacjonarne (do kół zdjętych z pojazdu),
- dostawne (do kół zamontowanych na pojeździe),
- aktywne (aplikatory proszku).
Zaletą wyważarek stacjonarnych jest duża dokładność pomiarów. Do wad należą: niemożliwość uwzględnienia niewyrównoważenia tarczy hamulcowej (bębna) i piasty koła oraz niewłaściwego centrowania koła w samochodzie, większa pracochłonność pomiarów, większy koszt wyważarek.
Zaletami wyważarek dostawnych są: mniejsza pracochłonność pomiarów, uwzględnienie niewyrównoważenia tarczy hamulcowej (bębna) i piasty koła, mniejszy koszt wyważarek. Zasadniczą wadą jest brak możliwości dokładnego ustalenia wielkości masy wyrównoważającej.
Ze względu na zakres zastosowania rozróżniamy wyważarki:
- motocyklowe,
- do kół samochodów osobowych,
- do kół samochodów ciężarowych,
- uniwersalne.
Ze względu na rozwiązanie konstrukcyjne układu pomiarowego wyważarki dzielą się na:
- mechaniczne,
- optyczne,
- elektryczne,
- elektroniczne,
- komputerowe.
W wyważarkach mechanicznych moment niewyrównoważenia dynamicznego koła jest zrównoważony najczęściej za pomocą ruchomych przeciwciężarów. Wyważarki te mają możliwość zmiany położenia osiowego i kątowego tych przeciwciężarów, co zezwala na ustawienie ich w położeniu prowadzącym do likwidacji niewyrównoważenia całego układu. W wyważarkach optycznych drgania wału przenoszone są przez układ dźwigniowo–przesłonkowy na lusterko, które steruje promieniem świetlnym. Promień ten, pada na wyskalowany ekran i wskazuje wartość oraz kątową lokalizację niewyrównoważenia. W wyważarkach elektrycznych drgania wału powodują zmiany napięcia w układach elektrycznych i są rejestrowane na odpowiednio wyskalowanych woltomierzach. Wyważarki elektroniczne wyposażone są w układ elektryczny przetwarzający drgania wału na proporcjonalny sygnał elektryczny oraz układ elektroniczny określający wartość i położenie niewyrównoważenia w płaszczyźnie wewnętrznej i zewnętrznej koła. Wyważarki komputerowe stanowią najnowszą odmianę wyważarek do kół jezdnych. W tego rodzaju wyważarkach zastosowano mikroprocesorowe sterowanie procesem pomiarowym. Dane dotyczące niewyrównoważenia zapisywane są w pamięci. Wartość niewyrównoważenia podawana jest w sposób cyfrowy, miejsce niewyrównoważenia wskazywane jest w sposób graficzny na wyświetlaczach lub monitorze. Proces pomiarowy jest w pełni zautomatyzowany. Wyważarki te charakteryzują się bardzo dużą dokładnością pomiaru.
Rys. 9. Elementy uchwytu stożkowego (źródło: Haweka): 1 – nakrętka, 2 – pierścień dociskowy, 3 – kołpak, 4÷6 – stożki centrujące, 7 – wałek, 8 – sprężyna.
2) Dokładność wyrównoważenia kół
Dokładność wyrównoważenia kół zależy od dokładności wykonania i stanu technicznego samej wyważarki, jakości wykonania i stanu obręczy oraz w dużym stopniu od precyzji mocowania koła na wale wyważarki, co jest związane z zastosowaniem odpowiedniego uchwytu. Nowoczesne wyważarki osiągają dokładność wyrównoważenia około 0,02 g. Nie odpowiada to rzeczywistej dokładności wyrównoważenia koła, gdyż wystąpią błędy jego mocowania na wale wyważarki. Przed założeniem koła na wyważarkę należy oczyścić obręcz (zaleca się stosowanie maszyn myjących koła) i sprawdzić jej stan. Otwory bazowe obręczy nie mogą być owalne i powinny mieć nieuszkodzoną powierzchnię. Obręcze wykonane ze stopów lekkich często wyposażone są w dodatkową wkładkę otworu centrującego (pierścień z tworzywa sztucznego). Umożliwia ona dopasowanie obręczy do różnych piast samochodowych. W przypadku odkształcenia tych pierścieni, należy je wymienić na nowe.
Rys.10. Uchwyt Duo Expert z tuleją rozprężną (źródło: Haweka): 1 – nakrętka, 2 – trzpieniowa tarcza, dociskowa, 3 – tuleja rozprężna, 4 – sprężyna, 5 – wałek, 6 – kołnierz.
Sposób mocowania koła na wale wyważarki ma podstawowy wpływ na dokładność wyrównoważenia. Skuteczne wyrównoważenie koła na wyważarce jest możliwe tylko w przypadku jego prawidłowego zamocowania i dokładnego wycentrowania. Sposób mocowania koła na wyważarce zależy od rozwiązania konstrukcyjnego tarczy koła. W samochodach najczęściej stosuje się następujące rodzaje tarcz (obręczy) kół:
- tarcze przelotowe (z otworem środkowym),
- tarcze nieprzelotowe (np. niektóre rozwiązania francuskie),
- tarcze dzielone płaskie, mocowane do piasty samochodów ciężarowych (np. Kamaz, Skoda).
We współczesnych samochodach tarcze kół centrowane są z reguły na otworze środkowym od wewnątrz. W taki sam sposób powinny być wówczas centrowane na wyważarce, to znaczy na stożku od środka – uchwyt stożkowy z nakrętką szybkomocującą (rys.9). Ponieważ stożek na wale musi się przesuwać, to oba te elementy wykonane są z określoną tolerancją. Jeżeli luz między otworem stożka a wałem wynosi 0,1 mm, powoduje to niedokładność wyrównoważenia około 10 g. Z tego powodu stosuje się określone tolerancje wykonania stożków i wałów, które zapewniają wymaganą dokładność wyrównoważenia. Podczas użytkowania wyważarki następuje stopniowe zużycie elementów centrujących, co prowadzi do zmniejszenia dokładności wykonywanych pomiarów. Rozwiązaniem, które eliminuje luz między elementami centrującymi, jest uchwyt Duo Expert firmy Haweka (rys. 10), w którym zastosowano pierścień rozprężny (tuleję centrującą). Zastosowany pierścień zmienia swoją średnicę zewnętrzną i wewnętrzną, zaciskając się bez luzu na wale i w otworze wewnętrznym obręczy. Ściskanie tego pierścienia powoduje zwiększanie jego średnicy zewnętrznej i zmniejszanie wewnętrznej. Taki uchwyt dobrze sprawdza się przy wyrównoważaniu obręczy stalowych oraz ze stopów lekkich (jest zalecany przez większość wytwórców samochodów osobowych). Ważnym elementem w uchwycie jest sprężyna środkowa, której sztywność ma duży wpływ na precyzję centrowania. Od sztywności sprężyny zależy siła wciskania elementu centrującego w otwór obręczy. Interesującym nowym rozwiązaniem systemu mocowania kół na wyważarkach jest uchwyt bezsprężynowy (rys. 11) Duo Matic I i uniwersalna płyta dociskowa QuickPlate stosowana do obręczy z różną liczbą otworów.
Rys. 11. Elementy uchwytu bezsprężynowego firmy Haweka.
W przypadku kół z obręczami nieprzelotowymi stosuje się uchwyty w postaci tarczy z trzpieniami (z rowkami prowadzącymi pod śruby lub nawierconymi otworami). Tarcza tego uchwytu ma zaznaczone średnice podziałowe, na które przesuwa się trzpienie. Ważnym elementem tego systemu jest pierścień centrujący dostosowany do konkretnych średnic nieprzelotowego otworu w obręczach. Brak tego pierścienia uniemożliwia dokładne wyrównoważenie koła.
Rys. 12. Uniwersalny uchwyt Uni Lug do mocowania kół z tarczami przelotowymi i nieprzelotowymi (źródło: Haweka).
W innych przypadkach, na przykład koła samochodów terenowych i dostawczych, często wykorzystuje się uchwyty typu Off-Road. Rozwiązanie takie jest stosowane w samochodach, które nie mają na piastach kołnierzy centrujących. Ich koła są centrowane na piaście tylko za pomocą śrub lub szpilek z nakrętkami, wobec tego uchwyt odwzorowuje takie mocowanie. Z powodu dużych prędkości jazdy, koła tych samochodów wymagają również dokładnego wyrównoważenia. Stosowany jest tutaj trzpieniowy uchwyt tarczowy, a stożek pełni jedynie rolę elementu ułatwiającego wprowadzenie trzpienia tarczy w otwory obręczy. Oferowane są również uchwyty z zabierakami szprychowymi przystosowane do kół motocyklowych. Jeszcze inne rodzaje uchwytów (np. tarcza ramienna) stosuje się do mocowania na wyważarkach kół samochodów ciężarowych.
Znane są też uchwyty uniwersalne, na przykład Uni Lug (rys. 12), do centrowania obręczy o konstrukcji zarówno przelotowej, jak i nieprzelotowej. Uchwyt ten jest bardzo precyzyjny, dzięki dokładnie frezowanym i szlifowanym obrotowym ramionom z trzpieniami. Ustawienie trzpieni na konkretną średnicę odbywa się bezstopniowo. Liczba ramion z trzpieniami zależy od ilości otworów w tarczy koła i zgodna jest z ich rozstawem, który mierzy się za pomocą specjalnej suwmiarki. Taki uchwyt może obejmować średnicę rozstawu śrub mocujących koło w granicach 95-215 mm. Uchwyt mocujący Uni Lug można przystosować do mocowania na 3, 4, 5, 6 lub 8 śrubach mocujących. Nową odmianę uchwytu można przystosować do wałów o różnych średnicach. Należy zastosować odpowiedni reduktor, który wchodzi w skład wyposażenia dodatkowego oferowanego przez wytwórcę.
Rys. 13. Uchwyty do mocowania kół na wyważarkach oferowane przez firmę Uni--Trol: a – uchwyt osobowy, b – uchwyt ciężarowy, c – uchwyt tarczowy szpilkowy, d – uchwyt motocyklowy.
Najdokładniejsze centrowanie uzyskuje się dla uchwytów zaprojektowanych indywidualnie dla danego typu tarczy (niektórzy producenci dostarczają uchwyty specjalne dla określonych marek samochodów, na przykład do samochodów Mercedes, BMW). Na rys. 13 przedstawiono przykładowo wybrane uchwyty do mocowania kół oferowane do wyważarek produkowanych przez firmę Uni-Trol.
Rys. 14. Sposoby mocowania ciężarków korekcyjnych w zależności od typu tarczy koła (źródło: Hofmann).
3) Wyposażenie uzupełniające
Produkowane są różne konstrukcje ciężarków do wyrównoważania kół jezdnych samochodów i motocykli. Można je podzielić na dwie grupy: ciężarki zaczepiane na brzegach obręczy i ciężarki przyklejane. O jakości ciężarków decyduje między innymi dokładność wykonania, pewne osadzenie sprężyny stalowej, jakość powłoki galwanicznej sprężyny, graniczny zakres temperatur kleju (dla ciężarków klejonych).
Starsze wersje ciężarków do wyrównoważania kół są wykonane z ołowiu z dodatkiem antymonu, a ich stalowa sprężyna jest przystosowana do mocowania na różnych typach obręczy kół. Nowe odmiany ciężarków wykonywane są z cynku lub stali. Ciężarki przyklejane zaleca się stosować w przypadku obręczy kół ze stopów lekkich. Różne sposoby mocowania ciężarków wyrównoważających w zależności od typu obręczy koła przedstawiono na rys. 14. Do wyrównoważania kół motocyklowych oraz kół samochodowych o nowej konstrukcji wewnętrznej (np. CTS) stosowane są ciężarki odmiennej konstrukcji. Przykłady różnych rozwiązań konstrukcyjnych ciężarków wyrównoważających pokazano na rys. 15.
Rys. 15. Rozwiązania konstrukcyjne ciężarków korekcyjnych: a – ciężarek z zalaną sprężyną mocującą, b – ciężarek ze sprężyną rozłączną, c – ciężarek przyklejany, d – ciężarek do kół typu CTS, e – ciężarek do szprychowych kół motocyklowych.
Do zakładania i wyjmowania ciężarków wyrównoważających stosuje się specjalne szczypce i ściskacze (dźwignie). Podczas zakładania ciężarka zaczepionego na brzegu obręczy niezbędne jest wykonanie następujących czynności:
- ściśnięcie boku opony i włożenie sprężyny,
- uniesienie sprężyny,
- wsunięcie ciężarka.
Na stanowisku do wyrównoważania kół niezbędne jest urządzenie do szybkiego demontażu i montażu ogumienia (rys.16). Najczęściej stosuje się urządzenia z napędem elektrohydraulicznym lub elektropneumatycznym, które wyciskają oponę z osadzenia, nie powodując uszkodzenia stopki opony ani obręczy koła. Jest to szczególnie ważne podczas demontażu opon bezdętkowych i stosowania obręczy ze stopów lekkich.
Rys.16. Przykłady urządzeń do demontażu opon (źródło: Space): a – do wymiany opon samochodów osobowych, b – do demontażu opon samochodów ciężarowych.
dr inż. Kazimierz Sitek
Komentarze (0)