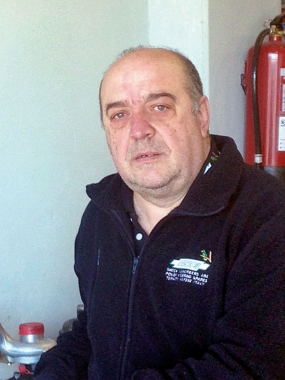
Przy zaangażowaniu stosunkowo niewielkich nakładów pracy i kilku podzespołów możemy zmienić złom zalegający w naszym magazynie w nową część i przyzwoitą marżę. W tym artykule i kilku kolejnych postaramy się w przystępny sposób przybliżyć czytelnikom proces regeneracji hydraulicznie wspomaganych układów kierowniczych.
Najbardziej tradycyjne układy kierownicze działały na zasadzie sparowania kolumny kierowniczej poprzez umiejscowiony na jej końcu zębnik z zębami listwy, której ruch wzdłużny przekładał się ciągnięcie lub pchanie drążków, a w rezultacie obracanie piast wokół ich prostopadłych osi. Gdy tylko pojazdy stawały się cięższe, a koła i opony większe, skręcanie stawało się coraz trudniejsze – pojawiła się konieczność zastosowania wspomagania i jak to często bywa, pojawiło się mnóstwo najróżniejszych rozwiązań. Najprostszym z nich jest układ zębnik-zębatka, który w skrócie działa następująco. Olej ze zbiornika zasysany jest przez pompę do komory zębnika, zębnik oddziałuje mechanicznie na zębatkę listwy, ale jednocześnie pełni rolę rozdzielacza, ponieważ obracając się, steruje umiejscowionym w nim zaworem, dystrybuując olej w jednym lub drugim kierunku oraz, poprzez przewód powrotny, zwraca niewykorzystany olej do zbiornika.
Jeśli skręcamy kierownicą w prawo, zębnik obraca się w prawo, otwiera mocniej zawór, co pozwala większej objętości oleju dostać się na lewą stronę cylindra przekładni, który popycha tłok zamontowany na listwie w prawą stronę, wspierając w ten sposób skręcanie. Olej zgromadzony w przekładni na prawo od tłoka powraca do komory rozdzielacza, a następnie do zbiornika. Co istotne, większość oleju powraca do zbiornika, nie będąc w ogóle wykorzystana – oznacza to, że efektywność tego systemu nie jest duża, ale taki był cel konstruktorów, bo układ służy do wspomagania kierowania samochodem, a nie wózkiem widłowym.
Niska wydajność systemu nie pozostaje obojętna na koszty eksploatacji samochodu (większe zużycie paliwa), stąd trend wprowadzania układów wspomaganych elektrycznie, ale tym zagadnieniem zajmiemy się dopiero w jednym z późniejszych artykułów.
Olej, starzejąc się, traci swoje właściwości fizyczne i chemiczne; uszczelki tracą swoją elastyczność, pozwalając wydobywać się olejowi na zewnątrz, a wodzie dostawać się do środka i tworzyć szlam. Pierścienie teflonowe na rozdzielaczu i tłoku zmniejszają swą szczelność, co pociąga za sobą spadek efektywności systemu, aż do jego całkowitej niewydolności skutkującej brakiem wspomagania. Listwa zębata utlenia się, na skutek uderzeń zęby się wyrabiają, więc okresowa kontrola jest wskazana. Czasem może okazać się niezbędna wymiana przekładni. Postawmy zatem kluczowe pytanie, dlaczego nie zregenerować zużytej przekładni i otrzymać za nią pieniądze, zamiast wydawać je na zakup nowej?
Aby dowiedzieć się, jak to prawidłowo zrobić, odwiedzamy Centrum Badawcze EMMETEC mieszczące się w Ternate w Lombardii, 10 km od lotniska Mediolan Malpensa, gdzie Pan Fidel Pardo (fot. 1), jeden z głównych specjalistów sektora regeneracji, objaśnia nam, jak regenerować przekładnie kierownicze TRW. W celu uproszczenia wyjaśnień w niniejszym tekście będziemy posługiwali się nazewnictwem i numeracją narzędzi firmy EMMETEC.
Organizacja stanowiska pracy
Hydraulicznie wspomagane układy kierownicze, jak żaden inny podzespół, wymagają absolutnej czystości, ale zazwyczaj do warsztatu trafiają ubrudzone olejem, pełne szlamu, błota i innych zanieczyszczeń. Pierwszą czynnością, jaką należy wykonać, jest zatem usunięcie oleju i następnie wyczyszczenie przekładni w myjce oraz wysuszenie jej przy pomocy sprężonego powietrza, aż do usunięcia ostatnich cząstek. Aby praca wykonana była idealnie, zaleca się rozłożyć przekładnię na stole roboczym na części pierwsze, aby doczyścić każdą część, a następnie przenieść je na inny stół, który powinien być sterylnie czysty, gdzie przekładnia będzie mogła być ponownie złożona. Oddzielenie demontażu od montażu to żelazna zasada procesu regeneracji, której nie powinno się łamać pod żadnym pozorem.
Rozbiórka
- Jeśli olej, który usuwaliśmy z przekładni, jest mocno zanieczyszczony, zawiera szlam, drobinki i kurz, wymagane jest zdemontowanie metalowych przewodów olejowych łączących komorę rozdzielacza z komorami przekładni po obu stronach tłoka. Należy jednak pamiętać przed zdemontowaniem tych elementów o zaznaczeniu ich pierwotnego położenia, aby możliwe było ich prawidłowe ponowne zamontowanie.
- Przy pomocy specjalnych szczypców ściągamy pierścień zabezpieczający SEGER (fot. 3).
- Następnie zdejmujemy nakrętkę (fot. 4) zaślepiającą kamień dociskowy (podporę) listwy, ale jako że przeważnie jest ona sfazowana i istnieje duże ryzyko uszkodzenia gwintu, należy odkręcać ją bardzo powoli, tyle ile możliwe, a następnie usunąć zadziory i nierówności wynikłe z fazowania przy pomocy wiertła lub gwintownika, wyczyścić, używając sprężonego powietrza i ostatecznie zdjąć nakrętkę. W następnej kolejności wyciągamy sprężynkę regulacyjną i docisk listwy (fot. 5), a następnie go sprawdzamy. Jeśli jest wyrobiony, wymieniamy go. Jeśli nie mamy zamiennej podpory, możemy wytoczyć na obwodzie starej rowek na o-ring w celu skasowania luzu. W przeciwnym razie, pozostawiając starą podporę z luzami, narażamy kierowcę na dokuczliwe stukanie podczas jazdy po nierównościach.
- Jeśli zamiast podpory listwy w przekładni występuje ślizg pod kamień, zwany potocznie „półksiężycem”, należy go bezwzględnie wymienić na nowy.
- Przy pomocy niezbyt ostrego dłuta otwieramy korek zakrywający łożysko rozdzielacza (fot. 6) i zabezpieczający je pierścień SEGER.
- Wyciągamy śrubę rozdzielacza przy pomocy klucza nasadkowego (fot. 7). Ta operacja musi być wykonana z drążkami kierowniczymi wkręconymi do przekładni, aby dawały opór, w przeciwnym razie istnieje ryzyko ukręcenia wałka skrętnego w rozdzielaczu. Następnie przy pomocy miękkiego młotka wysuwamy rozdzielacz z komory (fot. 8) wraz z tuleją oraz dolnym uszczelniaczem.
- Odkręcamy drążki kierownicze.
- Za pomocą specjalnych szczypców obracamy tuleję zamykającą (fot. 9) z listwy, ściągając SEGER od strony, z której jest zagięty. Jeśli przez pomyłkę przekręcimy w odwrotną stronę, aż do ukazania się zakończenia SEGERA, należy wcisnąć go w jego miejsce, kręcąc tuleją zamykającą i zacząć od początku kręcić w dobrym kierunku.
- Przy pomocy miękkiego młotka wybijamy listwę z obudowy (fot. 10). Tuleja zamykająca wyskoczy wraz z listwą, ściągamy z niej uszczelniacz olejowy i o-ring i sprawdzamy, czy nie jest odkształcona. Jeśli tak, to należy ją wymienić.
- Przy pomocy wałka teflonowego specjalnie uformowanego w taki sposób, aby uderzał jedynie w zewnętrzny pierścień wyciągamy łożysko rozdzielacza, a za pomocą nasadki 17 mm wyciągamy tuleję i drugi uszczelniacz (fot. 12).
- Przy użyciu ściągacza wyjmujemy główny uszczelniacz olejowy ciśnieniowy z korpusu przekładni (fot. 13). Aby zapobiec powstaniu zarysowań wewnątrz korpusu przekładni, zaleca się używanie ściągaczy specjalnie zaprojektowanych do przekładni – w tym przypadku posłużyliśmy się EMMETEC Z-09000 do uszczelniaczy o średnicach wewnętrznych między 20 a 30 mm. Aby uprościć tę czynność, zaleca się: wyregulować pozycję stożka na głębokość oryginalnie zamontowanego uszczelniacza oraz wyregulowanie łapek na szerokość zbliżoną do średnicy wewnętrznej uszczelniacza (czyli średnicy listwy). Wszystko to w celu jak najkrótszego operowania wewnątrz obudowy.
- Należy dokładnie sprawdzić wnętrze obudowy przekładni (fot. 14) i jeśli występują jakieś znaczniejsze zarysowania lub inne oznaki zużycia, szczególnie w środkowej części w obrębie pracy tłoka, nie należy jej niestety dalej używać. Jedynym rozwiązaniem jest wykorzystanie obudowy z innej przekładni tego samego typu.
- Przy użyciu szperacza Z-19001 możliwe jest zajrzenie w każdy zakątek obudowy.
- Następnie umieszczamy listwę w tokarce, aby sprawdzić, czy nie jest odkształcona i czyścimy jej powierzchnię bardzo drobnym papierem ściernym, aby usunąć naloty rdzy. Jeśli rdza wdarła się głębiej w materiał, należy go usunąć przez szlifowanie, co omówimy szerzej w kolejnym artykule.
- Sprawdzamy ogranicznik (bolec) i jego mocowanie w rozdzielaczu (fot. 15), ponieważ nie mogą tam wystąpić żadne luzy.
Części zamienne
Wszystkie pierścienie teflonowe, o-ringi i uszczelniacze powinny być wymienione w procesie regeneracji. Można posłużyć się gotowym zestawem naprawczym, ale nie zawsze jest to skuteczne. Zdarza się bowiem, że w „takich samych” przekładniach występują na tłoku inne pary pierścienia teflonowego z o-ringiem od tych zwartych w oryginalnym zestawie naprawczym, co spowodować może wstrzymanie pracy. Z tego powodu zaleca się zbudowanie małego zapasu podstawowych typów o-ringów, pierścieni teflonowych i uszczelniaczy – mała inwestycja zamortyzuje się szybko, ponieważ praca będzie przebiegała bez zakłóceń, bez straty czasu i pieniędzy na nagłe przesyłki ekspresowe.
Podzespoły należy przechowywać, unikając narażania na działanie pyłu, światła i wilgoci, a także dbając o to, aby ich nie pomieszać i nie zgniatać. EMMETEC oferuje kompletny system magazynowy Stand-by (fot. 16), w którym każdy element posiada własną szufladkę z naklejką zawierającą indeks produktu oraz jego wymiary. Wygodnym narzędziem do łatwego doboru uszczelniaczy, o-ringów i teflonów jest komplet stożków Z-11000, dzięki któremu rozmiar części określamy błyskawicznie, wrzucając ją na odpowiedni stożek i odczytując średnicę.
Bardzo mocno zaleca się stosowanie wysokiej jakości podzespołów, ponieważ różnica cenowa między tanim uszczelniaczem a jakościowym nie jest istotna, jeśli na szali położymy stracony czas, dodatkowe koszty transportu i niezadowolenie wracającego z reklamacją klienta. W rzeczywistości przy regeneracji zalecamy używanie najlepszych komponentów, lepszych nawet od oryginałów, które projektowane są do prostszego uszczelniania nowych przekładni.
Składanie
- Ściskamy nieco przy pomocy prasy hydraulicznej mocowanie przegubów drążków kierowniczych, aby zredukować luz.
- Usuwamy 4 stare pierścienie teflonowe z rozdzielacza (fot. 18) przy pomocy specjalnych wykałaczek Z-20001 lub Z-20007. Nigdy nie wolno używać do tego celu śrubokręta, ponieważ grozi to bezpowrotnym uszkodzeniem rowków, w których osadzone są teflony.
Zakładamy nowe pierścienie.
- Jako że teflony nie są elastyczne, aby je prawidłowo założyć, musimy użyć tulei kalibrujących typu Z-09060/Z-09062. Jeśli zbytnio rozciągniemy teflon i odkształcona jest jego średnica zewnętrzna (co zdarza się prawie zawsze), musimy go ścisnąć tuleją montażową typu Z-09050/Z-09064, jak pokazano na fot. 19 i pozostawić na około 10 minut.
- Następnie wymieniamy w ten sam sposób o-ring i teflon na tłoku (fot. 20). Teflon może być bardzo delikatnie założony ręcznie, ale aby nadać mu pierwotną średnicę zewnętrzną, należy skalibrować go właściwą tuleją (fot.21).
- Jeśli wcześniej odłączaliśmy, to teraz musimy zamontować z powrotem stalowe przewody olejowe łączące komorę rozdzielacza z obudową przekładni, wymieniając przy okazji miedziane podkładki i zwracając uwagę na prawidłowe położenie przewodów.
- Wprowadzamy listwę zębatą do obudowy, upewniając się dwukrotnie, czy tłok zapewnia odpowiednie tarcie: jeśli jest zbyt słabe, pierścień teflonowy nie zapewnia właściwego oddzielania komór; jeśli tarcie jest zbyt duże, średnica pierścienia przekracza właściwy rozmiar i skręcanie będzie wymagało używania zbyt dużej siły. Sięgamy więc do naszych zapasów części i dobieramy nieco mniejszy pierścień.
- Jeśli tuleja z rozdzielacza nie nosi znamion zużycia, możemy użyć ją ponownie (fot.22), używając miękkiego młotka i odpowiednio ukształtowanego wałka teflonowego. W przeciwnym razie tuleję należy wymienić.
- Zakładamy nowe uszczelniacze na rozdzielacz. Montujemy także łożysko, uderzając metalowym cylindrem tylko zewnętrzny jego pierścień (fot.23).
- Zakładamy pierścień zabezpieczający SEGER.
- Mocujemy wewnętrzny uszczelniacz w środku obudowy przy pomocy specjalnego dobijaka (na fot. 24 – Z-09700) i miękkiego młotka. Aby wsunąć listwę zębatą do środka i przeprowadzić zęby przez zamontowany przed chwilą uszczelniacz, nie naruszając jego elementu uszczelniającego, korzystamy z pomocy jednego z gamy 21 rozmiarów (komplet Z-09560 do wszystkich średnic listew) specjalnych ochraniaczy (fot. 25), nakładając to zrobione z bardzo cienkiego tworzywa narzędzie ciasno na listwę.
- Wprowadzamy listwę z założonym ochraniaczem do środka obudowy (fot. 26), przesuwamy ją przez uszczelniacz wewnętrzny i popychamy aż do końca. Należy pamiętać, aby nie ciągnąć listwy, ponieważ grozi to zmianą pozycji uszczelniacza. Na koniec ściągamy z listwy ochraniacz.
- Wymieniamy o-ring i uszczelniacz zewnętrzny, to jest na tulei zamykającej i wprowadzamy do obudowy przekładni przy użyciu specjalnego stożka montażowego ze stali nierdzewnej, aby nie uszkodzić nowego uszczelniacza.
- Wprowadzamy zagięty koniec pierścienia do jego mocowania na tulei zamykającej (fot. 27) i obracamy przy pomocy szczypców, aż cały pierścień zostanie wprowadzony i się schowa.
- Montujemy drążki. Spowoduje to ograniczenie zakresu ruchu listwy i zabezpieczy uszczelniacz wewnętrzny przed kontaktem z zębami listwy.
- Podczas gdy prawą ręką przesuwamy listwę, lewą wciskamy rozdzielacz do środka (fot. 28).
- Następnie zakładamy tuleję z tworzywa, uszczelniacz i SEGER.
- Wkładamy docisk listew, sprężynkę, smar i zakręcamy korek.
- Wkręcamy śrubę rozdzielacza i zakładamy kapsel.
Przedstawiliśmy tu w zarysie procedurę regeneracji przekładni kierowniczej. Naszych drogich Czytelników, zanim sami wezmą się za tę pracę, uprzejmie zachęcamy do przeczytania kolejnego artykułu, w którym szczegółowo przedstawimy podstawowe sztuczki ułatwiające pracę i pozwalające ominąć wiele niespodziewanych trudności.
Carlos Panzieri
konsultant techniczny
www.emmetec.com
Komentarze (0)